High-speed coiled material powder spray device, working method thereof and power spray production line
A technology of spraying device and powder coating, applied in spraying device, electrostatic spraying device, device for coating liquid on the surface, etc., can solve the problems of not getting good results and technical limitations, so as to improve the powdering effect and reduce the The effect of relative motion speed
- Summary
- Abstract
- Description
- Claims
- Application Information
AI Technical Summary
Problems solved by technology
Method used
Image
Examples
Embodiment 1
[0025] figure 1 It is a structural schematic diagram of the powder spraying device of the present invention.
[0026] Such as figure 1 As shown, the present embodiment 1 provides a powder spraying device, comprising: a powder spraying chamber 1 equipped with high-voltage static electricity; 2 moving in the same direction; and the powder spray chamber 1 is suitable for forming a corona space, so that the powder coating can be electrostatically adsorbed on the surface of the workpiece.
[0027] Optionally, the workpiece can be but not limited to color steel coils and color aluminum coils, and can be continuously conveyed through a conveying line.
[0028] Preferably, the movement speed of the powder coating and the workpiece can be kept in the same direction by controlling the air velocity.
[0029] Experiments have found that powder electrostatic spraying can be applied normally at a slow speed, but it is difficult for the powder to be efficiently adsorbed to the substrate a...
Embodiment 2
[0054] On the basis of Example 1, this Example 2 provides a working method of a powder coating device, the powder coating device is suitable for driving the powder coating and the moving workpiece to move in the same direction through the air flow, and the powder coating is adsorbed by static electricity on the workpiece surface.
[0055] For the specific structure and implementation process of the powder spraying device, please refer to the relevant discussion of Embodiment 1, and details will not be repeated here.
Embodiment 3
[0057] image 3 It is a structural schematic diagram of the powder spraying production line of the present invention.
[0058] On the basis of Example 1, such as image 3 As shown, the present embodiment 3 provides a powder coating production line, including: a conveyor line 7 for transporting workpieces 2 and several powder coating devices 8 as described above; The side of the line 7 is used to powder coat the moving workpiece 2 respectively.
[0059] Optionally, the workpiece may be, but not limited to, continuous workpieces such as color steel coils and color aluminum coils conveyed by a conveyor line. Each powder coating device can be installed on both sides of the workpiece to perform powder coating on both sides. When the sprayed surface of the workpiece needs to be sprayed in multiple layers (for example, primer and flour need to be coated), multiple powder spraying devices can be installed on the side of the sprayed surface of the workpiece along the moving directio...
PUM
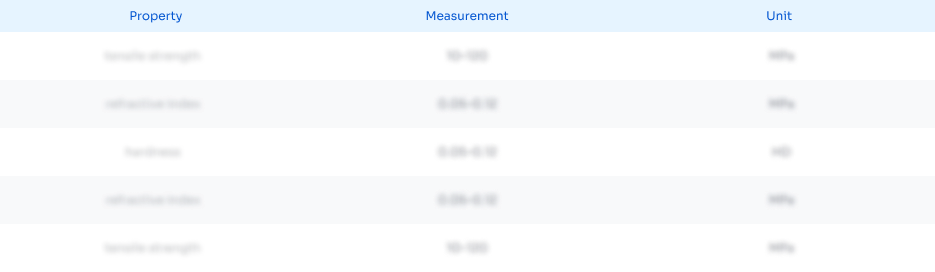
Abstract
Description
Claims
Application Information

- R&D Engineer
- R&D Manager
- IP Professional
- Industry Leading Data Capabilities
- Powerful AI technology
- Patent DNA Extraction
Browse by: Latest US Patents, China's latest patents, Technical Efficacy Thesaurus, Application Domain, Technology Topic, Popular Technical Reports.
© 2024 PatSnap. All rights reserved.Legal|Privacy policy|Modern Slavery Act Transparency Statement|Sitemap|About US| Contact US: help@patsnap.com