Polyphenylene sulfide resin production process
A technology of polyphenylene sulfide resin and production process, which is applied in the field of production process of polyphenylene sulfide resin, and can solve the problem of irregular polyphenylene sulfide resin particles, small polyphenylene sulfide resin particles, and polyphenylene sulfide resin molding Difficulties and other problems, to achieve the effect of improving particle forming rate, improving purity and improving performance characteristics
- Summary
- Abstract
- Description
- Claims
- Application Information
AI Technical Summary
Problems solved by technology
Method used
Examples
Embodiment 1
[0030] The production process of polyphenylene sulfide resin:
[0031] (1) Add sodium sulfide and N-methylpyrrolidone containing 5 crystal waters into the dehydration kettle, of which Na 2 The molar ratio of S:NMP is 1.0:1.8. Under the condition of feeding nitrogen, the temperature in the reactor is raised to 210°C at a rate of 1°C / min, and the dehydration time is 300min;
[0032] (2) In the dehydration system, after adding p-dichlorobenzene, add a certain amount of NMP solvent, so that the Na in the polymerization system 2 S:p-DCB:H 2 The molar ratio of O:NMP is 1.0:0.98:1.6:3.8. Nitrogen is introduced into the synthesis system, and the air in the polymerization system is replaced to seal the polymerization reaction system, and then the polymerization system is heated up. When the temperature rises to the low temperature stage At this stage, the temperature is 210°C and the pressure is 3kg / cm 2 , time 210min, when the low-temperature stage heat preservation is over, the te...
Embodiment 2
[0042] (1) Add sodium sulfide and N-methylpyrrolidone containing 5 crystal waters into the dehydration kettle, of which Na 2 The molar ratio of S:NMP is 1.0:3.8, under the condition of feeding nitrogen, the temperature in the reactor is raised to 214°C at a speed of 3°C / min, and the dehydration time is 240min;
[0043] (2) After adding p-dichlorobenzene in the dehydration system, add a certain amount of NMP solvent, so that the Na in the polymerization system 2 S:p-DCB:H 2 The molar ratio of O:NMP is 1.0:1.08:1.9:4.8. Nitrogen is introduced into the synthesis system, and the air in the polymerization system is replaced to seal the polymerization reaction system, and then the polymerization system is heated up. When the temperature rises to the low temperature stage At this stage, the temperature is 220°C and the pressure is 6kg / cm 2 , time 180min, when the low-temperature stage heat preservation is over, the temperature rises to the high-temperature polymerization stage at a...
Embodiment 3
[0053] (1) Add sodium sulfide and N-methylpyrrolidone containing 5 crystal waters into the dehydration kettle, of which Na 2 The molar ratio of S:NMP is 1.0:2.1. Under the condition of feeding nitrogen, the temperature in the reactor is raised to 211°C at a rate of 1.5°C / min, and the dehydration time is 255min;
[0054] (2) Add p-dichlorobenzene in the dehydration system and add a certain amount of NMP solvent so that Na in the polymerization system 2 S:p-DCB:H 2 The molar ratio of O:NMP is 1.0:1.0:1.63:4.1. Nitrogen is introduced into the synthesis system, and the air in the polymerization system is replaced to seal the polymerization reaction system, and then the polymerization system is heated up. When the temperature rises to the low temperature stage At this stage, the temperature is 212°C and the pressure is 3.5kg / cm 2 , time 191min, when the low-temperature stage heat preservation is over, the temperature rises to the high-temperature polymerization stage at a rate of...
PUM
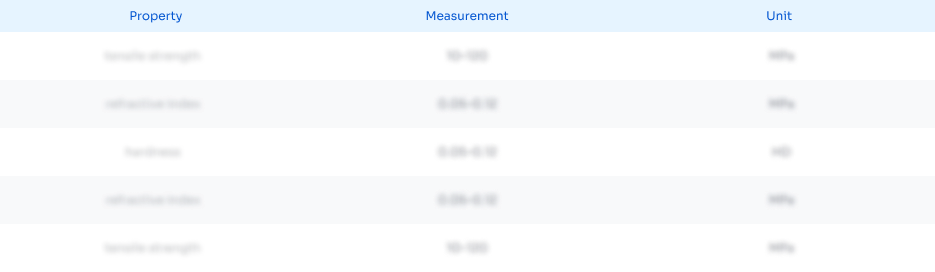
Abstract
Description
Claims
Application Information

- R&D
- Intellectual Property
- Life Sciences
- Materials
- Tech Scout
- Unparalleled Data Quality
- Higher Quality Content
- 60% Fewer Hallucinations
Browse by: Latest US Patents, China's latest patents, Technical Efficacy Thesaurus, Application Domain, Technology Topic, Popular Technical Reports.
© 2025 PatSnap. All rights reserved.Legal|Privacy policy|Modern Slavery Act Transparency Statement|Sitemap|About US| Contact US: help@patsnap.com