A utility boiler flue gas waste heat utilization system
A technology for flue gas waste heat and power plant boilers, applied in indirect heat exchangers, lighting and heating equipment, etc., can solve the problems affecting the efficiency of heat exchange and the decline of heat exchange capacity, and achieve smooth flow, suppression of backflow, and uniform distribution. Effect
- Summary
- Abstract
- Description
- Claims
- Application Information
AI Technical Summary
Problems solved by technology
Method used
Image
Examples
Embodiment Construction
[0032] A boiler flue gas waste heat utilization system. The waste heat utilization system includes a heat pipe 11, a flue gas channel 1 and an air channel 2. The heat pipe 11 includes an evaporation end 111 and a condensation end 112, and the condensation end 112 is arranged in the air In the channel 12, the evaporation end 11 is arranged in the flue. The evaporation end 111 absorbs the waste heat of the flue gas in the boiler flue, and transfers the heat to the air in the air passage 12 through the condensation end 112. The preheated air enters the boiler furnace to support combustion.
[0033] During operation, the heat pipe of the present invention absorbs heat from the flue gas through the evaporating end 111, and then releases the heat to the air at the condensing end, the fluid is condensed, and then enters the evaporating end 111 by the action of gravity.
[0034] During the operation of the waste heat utilization device, there is uneven fluid distribution, and because the ...
PUM
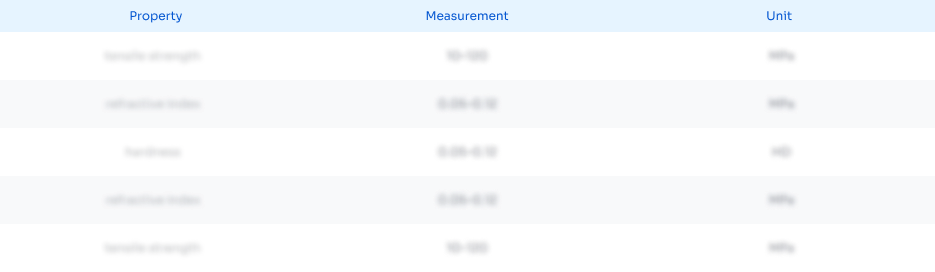
Abstract
Description
Claims
Application Information

- R&D
- Intellectual Property
- Life Sciences
- Materials
- Tech Scout
- Unparalleled Data Quality
- Higher Quality Content
- 60% Fewer Hallucinations
Browse by: Latest US Patents, China's latest patents, Technical Efficacy Thesaurus, Application Domain, Technology Topic, Popular Technical Reports.
© 2025 PatSnap. All rights reserved.Legal|Privacy policy|Modern Slavery Act Transparency Statement|Sitemap|About US| Contact US: help@patsnap.com