Phase change heat sink manufacturing process
A manufacturing process and radiator technology, which can be used in cooling/ventilation/heating transformation, modification with liquid cooling, electrical components, etc., which can solve the problems of large horizontal temperature difference and vertical temperature difference, poor heat dissipation effect, and inability to transfer heat evenly. To achieve the effect of reducing the difficulty of operation
- Summary
- Abstract
- Description
- Claims
- Application Information
AI Technical Summary
Problems solved by technology
Method used
Image
Examples
Embodiment Construction
[0031] The present invention will be described in further detail below in conjunction with the accompanying drawings.
[0032] A manufacturing process of a phase change radiator. The operator first creates an installation groove on the installation surface of the radiator body, and then embeds the PCB board in the installation groove and fixes it, and the bottom surface of the PCB board and the groove bottom of the installation groove A closed cavity is formed, and then the air in the closed cavity is drawn out through the connecting pipe preformed on the radiator body, and then the phase change medium is poured into the closed cavity through the connecting pipe, and finally the connecting pipe is closed, so that the radiator The main body, the closed cavity and the phase-change medium together form a uniform-temperature phase-change heat dissipation structure.
[0033] The specific steps are described below:
[0034] The body of the S1 radiator has a square structure. The op...
PUM
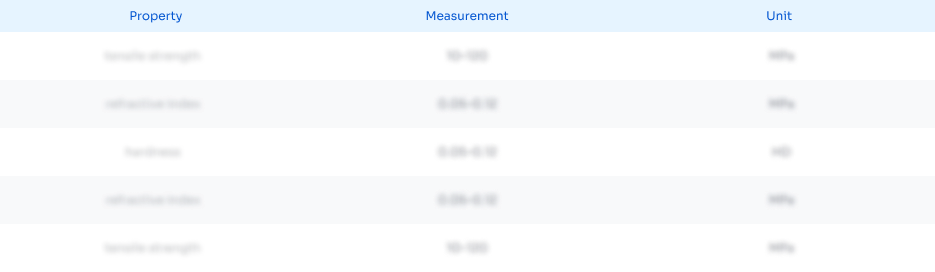
Abstract
Description
Claims
Application Information

- R&D
- Intellectual Property
- Life Sciences
- Materials
- Tech Scout
- Unparalleled Data Quality
- Higher Quality Content
- 60% Fewer Hallucinations
Browse by: Latest US Patents, China's latest patents, Technical Efficacy Thesaurus, Application Domain, Technology Topic, Popular Technical Reports.
© 2025 PatSnap. All rights reserved.Legal|Privacy policy|Modern Slavery Act Transparency Statement|Sitemap|About US| Contact US: help@patsnap.com