Low-concentration flue gas desulfurization method for hydroelectric silicon smelting
A low-concentration, flue gas technology, applied in separation methods, chemical instruments and methods, and dispersed particle separation, can solve problems such as high exhaust gas volume and sulfur content, hinder system chemical reactions, and cause great harm to desulfurization systems, so as to reduce waste liquid generation, improve desulfurization efficiency, and facilitate filtration and precipitation
- Summary
- Abstract
- Description
- Claims
- Application Information
AI Technical Summary
Problems solved by technology
Method used
Examples
Embodiment 1
[0035] A method for desulfurizing low-concentration flue gas from hydropower silicon smelting, comprising the following steps:
[0036] 1) Preparation of the absorption slurry: fully mix the desulfurization adsorbent ground to 325 mesh with water to obtain the absorption slurry; the amount of water added to the absorption slurry should be controlled so that the solid content in the absorption slurry does not exceed 8%; The desulfurization adsorbent includes the following raw materials in parts by weight: 50 parts of limestone and 0.1 part of oleic acid.
[0037] 2) Absorption of acid gas: When the flue gas from hydropower silicon smelting enters the desulfurization system, the absorption slurry and the flue gas are fully contacted in the desulfurization tower, including the top spraying and bottom stirring of the absorption slurry, and the absorption slurry is discharged from the top of the desulfurization tower Spraying, countercurrent contact with the flue gas, and then cont...
Embodiment 2
[0040] A method for desulfurizing low-concentration flue gas from hydropower silicon smelting, comprising the following steps:
[0041] 1) Preparation of absorption slurry: fully mix the desulfurization adsorbent ground to 400 mesh with water to obtain the absorption slurry; the amount of water added to the absorption slurry should be controlled so that the solid content in the absorption slurry does not exceed 7%;
[0042] The desulfurization adsorbent includes the following raw materials in parts by weight: 100 parts of limestone, 1 part of oleic acid, 2 parts of polydimethylsiloxane, 0.5 part of sodium polyphosphate, and 0.5 part of sodium hexametaphosphate.
[0043] 2) Absorption of acid gas: When the flue gas from hydropower silicon smelting enters the desulfurization system, the absorption slurry and the flue gas are fully contacted in the desulfurization tower, including the top spraying and bottom stirring of the absorption slurry, and the absorption slurry is discharge...
Embodiment 3
[0046] A method for desulfurizing low-concentration flue gas from hydropower silicon smelting, comprising the following steps:
[0047] 1) Preparation of absorption slurry: fully mix the desulfurization adsorbent ground to 325 mesh with water to obtain the absorption slurry; the amount of water added to the absorption slurry should be controlled to control the solid content of the absorption slurry to no more than 6%;
[0048] The desulfurization adsorbent includes the following raw materials in parts by weight: 75 parts of limestone, 0.5 part of oleic acid, 1 part of polydimethylsiloxane, 0.3 part of sodium polyphosphate, 0.3 part of sodium hexametaphosphate, and 8 parts of activated carbon. The activated carbon includes the following raw materials in weight percentage: 10% industrial silicon slag, 90% plant-derived activated carbon; the plant-derived activated carbon is coconut shell activated carbon, Yunnan sticky wood bark activated carbon, and Yunnan sycamore fruit activat...
PUM
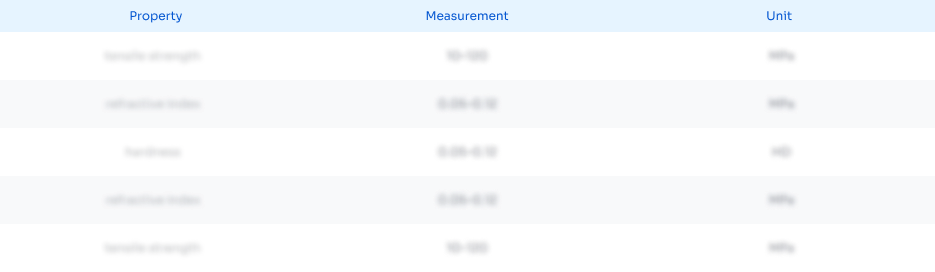
Abstract
Description
Claims
Application Information

- R&D
- Intellectual Property
- Life Sciences
- Materials
- Tech Scout
- Unparalleled Data Quality
- Higher Quality Content
- 60% Fewer Hallucinations
Browse by: Latest US Patents, China's latest patents, Technical Efficacy Thesaurus, Application Domain, Technology Topic, Popular Technical Reports.
© 2025 PatSnap. All rights reserved.Legal|Privacy policy|Modern Slavery Act Transparency Statement|Sitemap|About US| Contact US: help@patsnap.com