Method for preparing cellulose ethers, cellulose ethers prepared by said method and architectural finishing material comprising same
A technology of cellulose ether and cellulose, applied in the field of preparation of cellulose ether, cellulose ether prepared by said preparation and building decoration materials containing it, to achieve the effects of improving surface operability and improving processing efficiency
- Summary
- Abstract
- Description
- Claims
- Application Information
AI Technical Summary
Problems solved by technology
Method used
Image
Examples
preparation example Construction
[0027] The present invention relates to a preparation method of cellulose ether, the cellulose ether prepared by the method and building decoration materials containing it, wherein the preparation method of the cellulose ether comprises the following steps: (1) by making the cellulose reacting with an alkalizing agent to obtain alkalized cellulose; (2) obtaining cellulose ether in a slurry state by subjecting the alkalized cellulose to an etherification reaction; and (3) to complete the ether Surfactants are added to the cellulose ether in the slurry state after chemical reaction.
[0028] First, the preparation method of the cellulose ether is specifically reviewed step by step as follows.
[0029] (1) The step of obtaining alkalized cellulose
[0030] This step is a step of obtaining alkalized cellulose by reacting cellulose with an alkalizing agent.
[0031] The step of obtaining the alkalized cellulose can be carried out under the reactants and reaction conditions common...
Embodiment 1
[0059] 1 kg of finely pulverized pulp (cellulose) (Rayonier, Ethenier-F), 1 kg of dimethyl ether as a reaction solvent and 50% by weight of sodium hydroxide as an alkalizing agent were added to the pressure reactor (Sanden Junyaku Industries) 1.25 kg of aqueous solution was stirred at 25° C. at 80 rpm for 60 minutes to obtain alkalized cellulose.
[0060] Next, after adding 125 g of ethylene oxide and 1 kg of methyl chloride into the reactor, react at 50° C. for 30 minutes, and then raise the temperature of the reactor to 90° C. at a rate of 2° C. / min. , carry out etherification reaction for 60 minutes.
[0061] Next, after the cellulose ether in the slurry state after the etherification reaction was completed was transferred to the slurry tank, 1 g of Pluronic RPE2520 (Basf) and water were added to the slurry tank as a nonionic surfactant. 7 L, then stirred at 100 rpm for one minute at 90 °C. At this time, the HLB value of the nonionic surfactant is 6, based on 100 parts by...
Embodiment 2
[0065]Cellulose ether was prepared by the same method as in Example 1 above except that 5 g of the nonionic surfactant was added. At this time, based on 100 parts by weight of cellulose, the added amount of the nonionic surfactant is equivalent to 0.5 parts by weight.
PUM
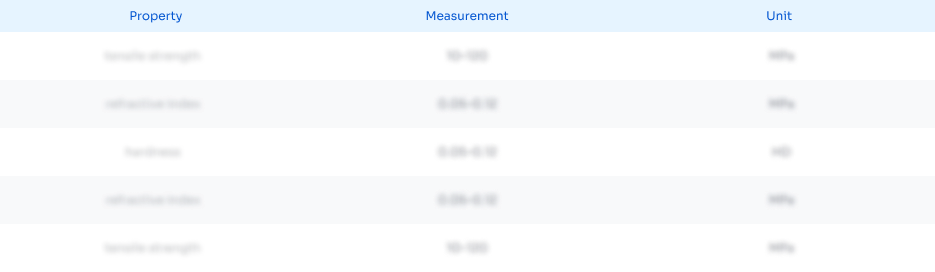
Abstract
Description
Claims
Application Information

- R&D
- Intellectual Property
- Life Sciences
- Materials
- Tech Scout
- Unparalleled Data Quality
- Higher Quality Content
- 60% Fewer Hallucinations
Browse by: Latest US Patents, China's latest patents, Technical Efficacy Thesaurus, Application Domain, Technology Topic, Popular Technical Reports.
© 2025 PatSnap. All rights reserved.Legal|Privacy policy|Modern Slavery Act Transparency Statement|Sitemap|About US| Contact US: help@patsnap.com