Cooling structure suitable for high-pressure turbines of gas turbines
A cooling structure, high-pressure turbine technology, applied in mechanical equipment, engine components, machines/engines, etc., can solve problems such as cooling of the pressure surface of the leakage channel, uneven distribution of pressure at the outlet of the slot, and difficulty in outflow from the pressure surface of the channel.
- Summary
- Abstract
- Description
- Claims
- Application Information
AI Technical Summary
Problems solved by technology
Method used
Image
Examples
Embodiment Construction
[0026] The present invention will be further described below in conjunction with specific embodiment and accompanying drawing, set forth more details in the following description so as to fully understand the present invention, but the present invention can obviously be implemented in many other ways different from this description, Those skilled in the art can make similar promotions and deductions based on actual application situations without violating the connotation of the present invention, so the content of this specific embodiment should not limit the protection scope of the present invention.
[0027] It should be noted that these and other subsequent drawings are only examples, which are not drawn according to the same scale, and should not be taken as limitations on the protection scope of the actual claims of the present invention.
[0028] Such as figure 1 As shown, the gap between the ring load-bearing wall 1 in the combustion chamber and the end surface of the b...
PUM
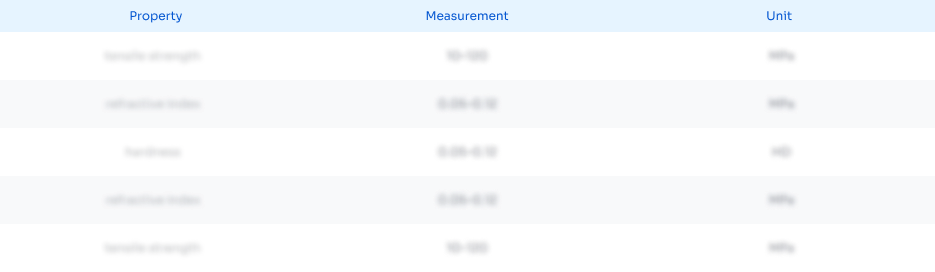
Abstract
Description
Claims
Application Information

- R&D Engineer
- R&D Manager
- IP Professional
- Industry Leading Data Capabilities
- Powerful AI technology
- Patent DNA Extraction
Browse by: Latest US Patents, China's latest patents, Technical Efficacy Thesaurus, Application Domain, Technology Topic, Popular Technical Reports.
© 2024 PatSnap. All rights reserved.Legal|Privacy policy|Modern Slavery Act Transparency Statement|Sitemap|About US| Contact US: help@patsnap.com