Production process of flame-retarding polystyrene foam board
A polystyrene foam and production process technology, applied in the field of building boards, can solve the problems of high process requirements, complex process, large amount of addition, etc., and achieve the effects of good flame retardant effect and simple processing technology.
- Summary
- Abstract
- Description
- Claims
- Application Information
AI Technical Summary
Problems solved by technology
Method used
Examples
Embodiment Construction
[0012] The present invention will be further described below with regard to specific embodiment:
[0013] A production process of a flame-retardant polystyrene foam board, spraying a flame retardant solution on the surface of the polystyrene foam board, and then using vacuum equipment to remove the The flame retardant solution is drawn off, the flame retardant solution is penetrated into the polystyrene foam board and coated on the surface of the polystyrene foam particles, and the polystyrene foam board is dried. Vacuuming equipment can be carried out with a vacuum pump and a vacuum tube. Among them, when spraying, high-pressure nozzles can be used to spray and then atomizing nozzles can be used to further spray, so that the flame retardant solution can fully soak into the polystyrene foam board, and the spraying time of each polystyrene foam board should not be less than 1min. The flame retardant solution includes a modified phosphorus-nitrogen flame retardant, a pH regulat...
PUM
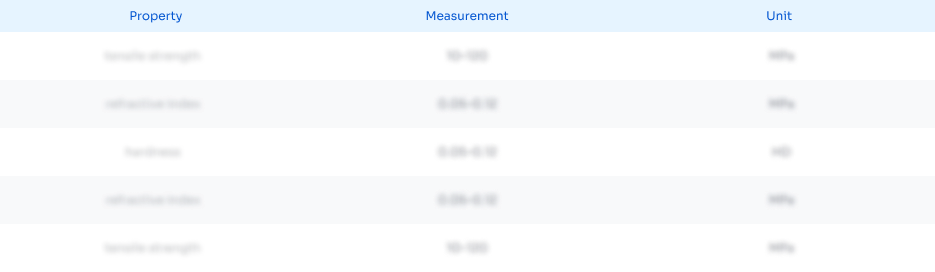
Abstract
Description
Claims
Application Information

- R&D
- Intellectual Property
- Life Sciences
- Materials
- Tech Scout
- Unparalleled Data Quality
- Higher Quality Content
- 60% Fewer Hallucinations
Browse by: Latest US Patents, China's latest patents, Technical Efficacy Thesaurus, Application Domain, Technology Topic, Popular Technical Reports.
© 2025 PatSnap. All rights reserved.Legal|Privacy policy|Modern Slavery Act Transparency Statement|Sitemap|About US| Contact US: help@patsnap.com