Machining process of end faces of gear
A processing technology and gear end technology, which is applied to the processing technology field of the gear end face, can solve the problems of easy tool wear, intermittent cutting, low work efficiency, etc., and achieve the effects of reducing production costs, improving work efficiency, and improving service life.
- Summary
- Abstract
- Description
- Claims
- Application Information
AI Technical Summary
Problems solved by technology
Method used
Image
Examples
Embodiment Construction
[0016] The following is further described in detail through specific implementation methods:
[0017] The reference signs in the drawings of the description include: the first motor 1, the second motor 2, the first screw mandrel 3, the tool holder 4, the workbench 5, the fixed seat 6, the transmission shaft 7, the incomplete gear 8, and the slide rod 9 , slip ring 10, slide rail 11, sleeve rod 12, support 13, rotating motor 14, second clamping rod 15, first rack 16, first gear 17, rotating shaft 18, first clamping rod 19, transmission Gear 20, transmission chain 21, limit block 22, swivel 24, screw rod 25, ratchet 26, slider 27, second rack 28, third rack 29, second gear 30.
[0018] A processing technology for a gear end face, comprising the following steps,
[0019] (1) Forging, according to the requirements of the drawing, the rough turning allowance is reserved on both ends of the forging;
[0020] (2) Normalizing, normalizing the forgings, eliminating the bad structure ...
PUM
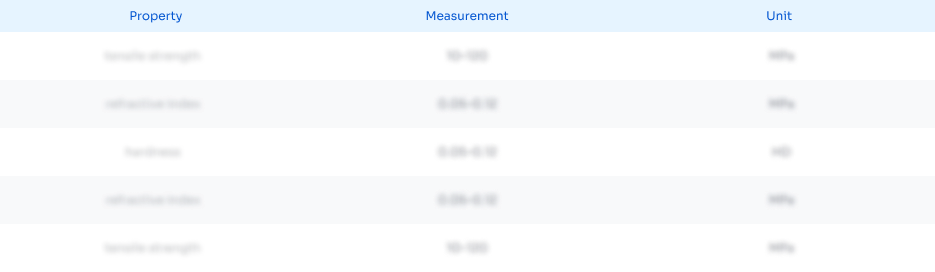
Abstract
Description
Claims
Application Information

- R&D
- Intellectual Property
- Life Sciences
- Materials
- Tech Scout
- Unparalleled Data Quality
- Higher Quality Content
- 60% Fewer Hallucinations
Browse by: Latest US Patents, China's latest patents, Technical Efficacy Thesaurus, Application Domain, Technology Topic, Popular Technical Reports.
© 2025 PatSnap. All rights reserved.Legal|Privacy policy|Modern Slavery Act Transparency Statement|Sitemap|About US| Contact US: help@patsnap.com