Nickel-net polyvinyl chloride foam attaching process used for processing table cloth
A technology of polyvinyl chloride and nickel mesh, which is applied in the direction of household components, applications, household appliances, etc., can solve the problems of high-quality use demand of consumers, easy aging of PVC materials, cumbersome production process, etc., to achieve strong practicability, The product has a strong sense of hierarchy and rich colors
- Summary
- Abstract
- Description
- Claims
- Application Information
AI Technical Summary
Problems solved by technology
Method used
Image
Examples
Embodiment 1
[0027] Example 1: The present invention is a nickel mesh polyvinyl chloride foam laminating process for processing tablecloths, including the steps of coating a polyvinyl chloride foam layer 1, printing, laminating, absorbing lines, cooling and setting, and winding. The polyvinyl chloride foam layer 1, which is made into a foamed polyvinyl chloride material by a calendering process, is compounded to form a polyvinyl chloride foam layer 1, after a first scraping and a second scraping. The thickness of the foam layer 1 is 200μm, the temperature is 175°C, and the speed is 20m / min. The printing step uses 30-mesh nickel mesh roll coating printing for color printing, and the bonding step uses direct bonding and The fusion paste combined with oblique pasting, the pattern suction step adopts vacuum high-pressure ceramic pattern roller to suck the pattern, the cooling and shaping are carried out by freezing water circulation, the traction tension of the winding step is 2.5kg / cm², and the...
Embodiment 2
[0035] Embodiment 2: The present invention is a nickel mesh polyvinyl chloride foam laminating process for processing tablecloths, including the steps of coating a polyvinyl chloride foam layer 1, printing, laminating, absorbing lines, cooling and setting, and winding. The polyvinyl chloride foam layer 1, which is made into a foamed polyvinyl chloride material by a calendering process, is compounded to form a polyvinyl chloride foam layer 1, after a first scraping and a second scraping. The thickness of the foam layer 1 is 520μm, the temperature is 220°C, and the speed is 25m / min. The printing step adopts 30-mesh metal nickel mesh roll coating printing for color printing, and the bonding step adopts direct bonding and The fusion paste combined with oblique pasting, the pattern suction step adopts vacuum high-pressure ceramic pattern roller to suck the pattern, the cooling and shaping are carried out by freezing water circulation, the traction tension of the winding step is 3.5kg...
Embodiment 3
[0043] Example 3: The present invention is a nickel mesh polyvinyl chloride foam laminating process for processing tablecloths, including the steps of coating a polyvinyl chloride foam layer 1, printing, laminating, absorbing lines, cooling and setting, and winding. The polyvinyl chloride foam layer 1, which is made into a foamed polyvinyl chloride material by a calendering process, is compounded to form a polyvinyl chloride foam layer 1, after a first scraping and a second scraping. The thickness of the foam layer 1 is 350μm, the temperature is 185°C, and the speed is 22m / min. The printing step uses 30-mesh metal nickel mesh roll coating printing for color printing, and the bonding step uses direct bonding and The fusion paste combined with oblique paste, the pattern suction step adopts vacuum high-pressure ceramic pattern roller to suck the pattern, the cooling and shaping are carried out by freezing water circulation, the traction tension of the winding step is 3.2kg / ㎝², and ...
PUM
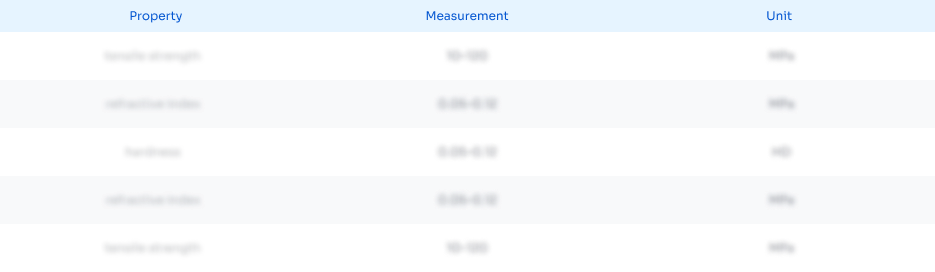
Abstract
Description
Claims
Application Information

- R&D
- Intellectual Property
- Life Sciences
- Materials
- Tech Scout
- Unparalleled Data Quality
- Higher Quality Content
- 60% Fewer Hallucinations
Browse by: Latest US Patents, China's latest patents, Technical Efficacy Thesaurus, Application Domain, Technology Topic, Popular Technical Reports.
© 2025 PatSnap. All rights reserved.Legal|Privacy policy|Modern Slavery Act Transparency Statement|Sitemap|About US| Contact US: help@patsnap.com