Flexible rope-driven coupling-free imitated human finger
A flexible cable-driven, non-coupling technology, applied in the field of human-like fingers, can solve problems such as the inability to perform finger "stretching" and "flicking" operations, the inability of fingertips to move independently and flexibly, and the application limitations are large. , to achieve the effect of reasonable internal structure layout, compact structure design and good flexibility
- Summary
- Abstract
- Description
- Claims
- Application Information
AI Technical Summary
Problems solved by technology
Method used
Image
Examples
Embodiment Construction
[0029] exist Figure 1 to Figure 8In the schematic diagram of the present invention shown, a through hole is provided in the middle part of the palm finger fixation 4 . The two sides that the palm and finger are fixed are respectively provided with the second limiting double roller group 13 and the proximal finger winding wheel 14, the proximal finger shaft 15 lower end is a square shaft, and the proximal finger shaft passes through the middle part of the second limiting double roller group successively. The through hole, the through hole in the middle part of the palm finger fixed plate, the square through hole in the middle part of the proximal finger winding wheel, and the square through hole in the middle part of the proximal finger winding wire is in interference connection with the square shaft at the lower end of the proximal finger shaft. A miniature bearing A24 and a miniature bearing B25 are respectively provided at the middle and upper ends of the proximal finger sh...
PUM
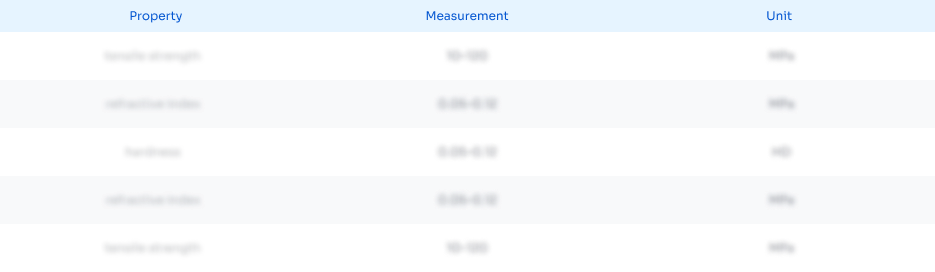
Abstract
Description
Claims
Application Information

- R&D
- Intellectual Property
- Life Sciences
- Materials
- Tech Scout
- Unparalleled Data Quality
- Higher Quality Content
- 60% Fewer Hallucinations
Browse by: Latest US Patents, China's latest patents, Technical Efficacy Thesaurus, Application Domain, Technology Topic, Popular Technical Reports.
© 2025 PatSnap. All rights reserved.Legal|Privacy policy|Modern Slavery Act Transparency Statement|Sitemap|About US| Contact US: help@patsnap.com