A side groove geometry optimization design method for compact tensile specimens with side grooves
A technology of compact stretching and geometric optimization, which is applied in the field of geometric optimization design of side grooves, can solve problems such as inability to ensure the consistency of crack front fracture parameter distribution, and achieve the effects of ensuring consistency, ensuring straightness, and improving accuracy
- Summary
- Abstract
- Description
- Claims
- Application Information
AI Technical Summary
Problems solved by technology
Method used
Image
Examples
Embodiment
[0052] A side groove geometric optimization design method for a compact tensile test piece with a side groove according to the present invention takes a CT specimen with a side groove with a thickness of 10 mm as an example to further illustrate the side groove optimization process, including the following steps:
[0053] (1) Define the properties of the material used in the tensile test piece in the finite element software, query the material booklet, use FGH96's elastic modulus E=214000MPa, Poisson's ratio u=0.28, and input it to the finite element through command flow or GUI in the software. Aeroengine powder alloy turbine disks are all nickel-based superalloys, and the fracture control parameter is the stress intensity factor K. At the same time, the potential defects and inclusions of powder alloy turbine disks also require damage tolerance design. Therefore, the selection of material properties of FGH96 is typical.
[0054] (2) In the finite element software, the 3-dime...
PUM
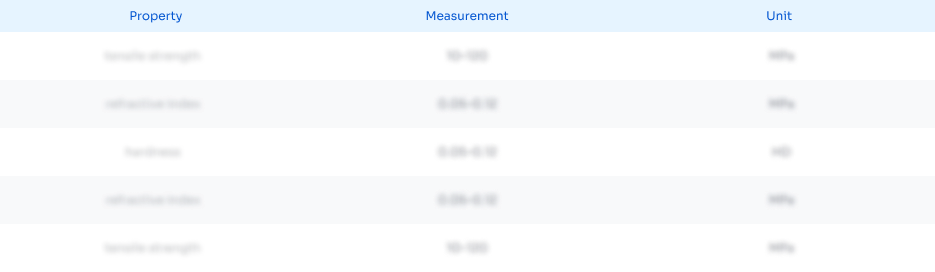
Abstract
Description
Claims
Application Information

- R&D
- Intellectual Property
- Life Sciences
- Materials
- Tech Scout
- Unparalleled Data Quality
- Higher Quality Content
- 60% Fewer Hallucinations
Browse by: Latest US Patents, China's latest patents, Technical Efficacy Thesaurus, Application Domain, Technology Topic, Popular Technical Reports.
© 2025 PatSnap. All rights reserved.Legal|Privacy policy|Modern Slavery Act Transparency Statement|Sitemap|About US| Contact US: help@patsnap.com