Die for cutting end of semi-elbow pipe sheet metal parts and application method thereof
A technology for sheet metal parts and pipe bends, which is applied in the field of molds for cutting ends of half-bend pipe sheet metal parts. Production quality and production efficiency, and the effect of reducing traffic intensity
- Summary
- Abstract
- Description
- Claims
- Application Information
AI Technical Summary
Problems solved by technology
Method used
Image
Examples
Embodiment Construction
[0019] The present invention will be further described in detail below in conjunction with the accompanying drawings and embodiments.
[0020] like Figure 1-Figure 3 As shown in the figure, a mold for cutting end of a half-bending sheet metal part includes a lower template 1 and an upper template 2. The upper surface of the lower template 1 is symmetrically provided with a guide column 3, and the middle of the upper surface of the lower template 1 is provided with a positioning seat 4, so The left and right side walls of the positioning seat 4 are symmetrically provided with positioning pieces 5, and the positioning pieces 5 ensure that the positioning pieces 5 and the cutting blade 11 are worn and replaced by sharpening. The lower surface of the upper template 2 is symmetrically provided with a guide sleeve 7 that cooperates with the guide column 3, the lower surface of the upper template 2 is provided with a blade seat 8 located just above the positioning seat 4, and a step...
PUM
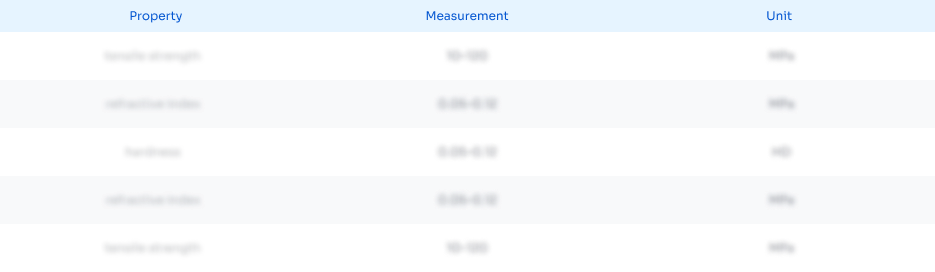
Abstract
Description
Claims
Application Information

- Generate Ideas
- Intellectual Property
- Life Sciences
- Materials
- Tech Scout
- Unparalleled Data Quality
- Higher Quality Content
- 60% Fewer Hallucinations
Browse by: Latest US Patents, China's latest patents, Technical Efficacy Thesaurus, Application Domain, Technology Topic, Popular Technical Reports.
© 2025 PatSnap. All rights reserved.Legal|Privacy policy|Modern Slavery Act Transparency Statement|Sitemap|About US| Contact US: help@patsnap.com