Lightweight aluminum-nickel composite busbar processing method
A processing method and busbar technology, applied in the direction of electrical components, circuits, battery pack parts, etc., can solve the problems of unstable welding strength, high contact resistance, high welding difficulty, etc., achieve flexible and changeable shape design, and improve use Lifespan, development-friendly effect
- Summary
- Abstract
- Description
- Claims
- Application Information
AI Technical Summary
Problems solved by technology
Method used
Image
Examples
specific Embodiment 1
[0041] step one,
[0042] Nickel strip: 1.5×115mm, HV1.0:90, 1 roll;
[0043] Aluminum strip: 4.0×115mm, HV1.0:18, 2 rolls;
[0044] The two strips are polished on the polishing machine, rinsed with hot water after polishing, and dried with hot air at the same time to ensure that there are no sundries, water spots, etc. on the surface;
[0045] Step two,
[0046] Composite is carried out on a two-roll rolling compound machine. The temperature of the nickel strip at the roll mouth is controlled at 250°C, the temperature deviation is ±5°C, and the aluminum strip is at room temperature. Before the strip enters the roll, the ammonia decomposition gas (N2, H2 ) for protection, the gas flow rate is controlled to 7Nm3 / h, the thickness of the composite machine outlet is 3.0mm, and the composite material tail is broken at 90° after the composite retrieving, there is no separation in the cross section, and the composite strength is qualified;
[0047] Step three,
[0048] After comp...
PUM
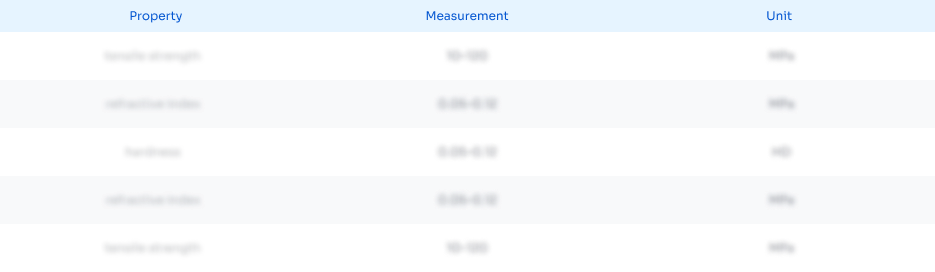
Abstract
Description
Claims
Application Information

- R&D Engineer
- R&D Manager
- IP Professional
- Industry Leading Data Capabilities
- Powerful AI technology
- Patent DNA Extraction
Browse by: Latest US Patents, China's latest patents, Technical Efficacy Thesaurus, Application Domain, Technology Topic, Popular Technical Reports.
© 2024 PatSnap. All rights reserved.Legal|Privacy policy|Modern Slavery Act Transparency Statement|Sitemap|About US| Contact US: help@patsnap.com