Method for rapidly improving temperature of annular cold flue gas
A technology of flue gas temperature and lifting ring, applied in the field of sintering, can solve the problem of flue gas temperature drop of the ring cooler, and achieve the effect of meeting the power generation requirements and increasing the power generation from sintering waste heat.
- Summary
- Abstract
- Description
- Claims
- Application Information
AI Technical Summary
Problems solved by technology
Method used
Examples
Embodiment 1
[0015] The method to quickly increase the temperature of the ring-cooled flue gas during a short-term shutdown is planned, and the specific plan is as follows:
[0016] 1) Before shutting down, reduce the ring cooling speed ratio to 0.02, adjust it to 0.38, increase the speed of the sintering machine by 0.1m / min (the speed of the sintering machine in normal production is 1.6-1.80.1m / min), and increase the thickness of the cloth layer of the ring cooler 30mm, the sintering end point is properly moved backward by 0.5 bellows.
[0017] 2) Before shutting down, it is necessary to appropriately increase the pressing degree of the machine head, and increase the pressing amount of the cloth at the machine head by 10mm, and stop the machine after the increased part of the pressing amount reaches the tail of the machine, so as to improve the heat storage effect of the material layer of the sintering machine.
[0018] 3) After shutting down, the frequency conversion of the main pump is ...
Embodiment 2
[0023] The method to quickly increase the temperature of the ring-cooled flue gas during an unplanned short-term shutdown is as follows:
[0024] 1) After shutting down, the frequency conversion of the main exhaust is immediately closed to 700r / min, and the main exhaust door is immediately closed to 0%, which can slow down the sintering vertical combustion speed and prolong the sintering time.
[0025] 2) After shutting down, the opening of the damper of the blower in the high temperature section of the ring cooler (2# blower) is reduced to 50%, and the damper is fully opened when it is in normal production.
[0026] 3) After starting up, the speed of the sintering machine is increased by 0.1-0.15m / min compared with the normal production speed, so that the burnt material can be poured out as soon as possible, and the temperature of the first and second ring cooling stages can be quickly recovered.
[0027] 4) After starting up, the sintering main exhaust door is opened based o...
PUM
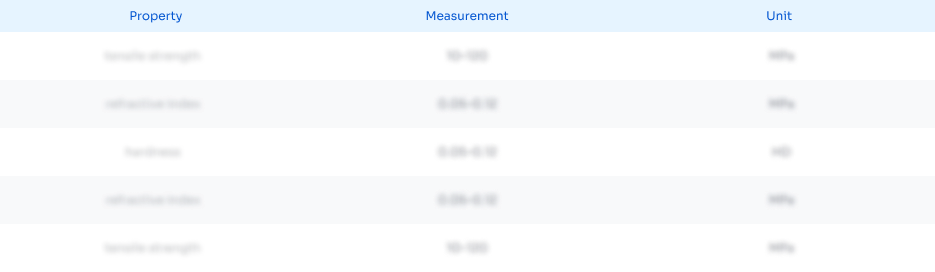
Abstract
Description
Claims
Application Information

- R&D
- Intellectual Property
- Life Sciences
- Materials
- Tech Scout
- Unparalleled Data Quality
- Higher Quality Content
- 60% Fewer Hallucinations
Browse by: Latest US Patents, China's latest patents, Technical Efficacy Thesaurus, Application Domain, Technology Topic, Popular Technical Reports.
© 2025 PatSnap. All rights reserved.Legal|Privacy policy|Modern Slavery Act Transparency Statement|Sitemap|About US| Contact US: help@patsnap.com