Automatic beveling machine
A chamfering machine, automatic technology, applied in the field of component processing, can solve the problems of low work efficiency, affecting the grinding accuracy, grinding wheel wear, etc., to achieve the effect of convenient adsorption of components, improve work efficiency and prolong service life
- Summary
- Abstract
- Description
- Claims
- Application Information
AI Technical Summary
Problems solved by technology
Method used
Image
Examples
Embodiment 1
[0035] Such as Figures 1 to 3 As shown, the automatic chamfering machine of this embodiment includes: a motor, a chamfering die 2, a three-axis moving mechanism 3, a vacuum chuck 4, a working platform 5 and a control system.
[0036] The vacuum chuck is connected to the vacuum generator through a solenoid valve; the solenoid valve is connected to a control system for controlling the tightness of the vacuum chuck. Automatically control the tightness of the vacuum chuck to ensure that the components can be firmly adsorbed and fixed or gently and stably released during the transfer and processing process, ensuring processing stability and precision.
[0037] Such as figure 1 As shown, as a preferred solution, a rectangular template 8 is provided on the working platform, and multiple mold cavities are arranged at equal intervals horizontally and vertically on the template 8, and multiple components are placed in the mold cavities of the template at fixed points. A plurality of ...
Embodiment 2
[0051] Such as Figure 8 and 9 As shown, compared with embodiment 1, an electric turntable 11 is set on the working platform of the present embodiment 1, and a plurality of chamfering molds 2 are evenly arranged on the electric turntable 11, and the first motor 1 driving the chamfering mold rotation is arranged on the electric turntable 11. The bottom of the turntable 11 drives the driving gear 12 to rotate, and the position of the corresponding chamfering mold below the turntable 11 is provided with a passive gear 13, and each chamfering mold 2 is fixedly connected with the passive gear 13 below the turntable 11, when the electric turntable 11 When driven by the servo motor to rotate at a specific angle, one of the driven gears 13 meshes with the driving gear 12, the first motor 1 rotates to drive the driving gear 12 to rotate, and the driving gear 12 drives the engaged passive gear 13 to rotate, and drives the chamfering mold 2 to rotate. The outer side of the turntable 11 ...
PUM
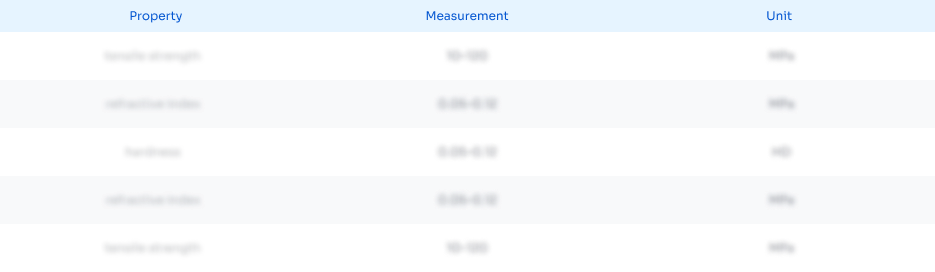
Abstract
Description
Claims
Application Information

- R&D Engineer
- R&D Manager
- IP Professional
- Industry Leading Data Capabilities
- Powerful AI technology
- Patent DNA Extraction
Browse by: Latest US Patents, China's latest patents, Technical Efficacy Thesaurus, Application Domain, Technology Topic, Popular Technical Reports.
© 2024 PatSnap. All rights reserved.Legal|Privacy policy|Modern Slavery Act Transparency Statement|Sitemap|About US| Contact US: help@patsnap.com