Preparation method of low-VOC flame-retardant composite filling material
A flame retardant composite and mixture technology, applied in the field of preparation of low VOC flame retardant composite fillers
- Summary
- Abstract
- Description
- Claims
- Application Information
AI Technical Summary
Problems solved by technology
Method used
Image
Examples
preparation example Construction
[0019] The application provides a method for preparing a low-VOC flame-retardant composite filler, comprising the following steps:
[0020] (1) Pulverize boehmite in a pulverizer, cross a 500-mesh sieve, then fully mix boehmite, bentonite, and basic calcium phosphate, and stir in a high-speed mixer for 40-60min to obtain mixture A; the temperature of the high-speed mixer is 70-90°C, the speed is 240-320r / min; the mass ratio of boehmite, bentonite and basic calcium phosphate is (60-80):(20-30):(10-16).
[0021] (2) Add octabromobisphenol S ether and nano-calcium silicate to the mixture A of step (1), fully stir and mix for 20-40min, and cool to room temperature to obtain a low-VOC flame-retardant composite filler; octabromobisphenol S ether , Nano calcium silicate, the mass ratio of mixture A is (40-60): (10-16): (60-80).
preparation example 1
[0023] (1) Take by weighing 600g boehmite, 200g bentonite, 100g basic calcium phosphate, pulverize boehmite in a pulverizer, cross a 500 mesh sieve, then fully mix boehmite, bentonite and basic calcium phosphate, Stir with a high-speed mixer for 40 minutes to obtain mixture A;
[0024] (2) Weigh 400g octabromobisphenol S ether, 100g nano-calcium silicate, and 600g mixture A, add octabromobisphenol S ether and nano-calcium silicate to step (1) mixture A, fully stir and mix for 20min, Cool to room temperature to obtain low VOC flame retardant composite filler P1.
[0025] Wherein the temperature of the high-speed mixer in the step (1) is 70° C., and the rotating speed is 240 r / min.
preparation example 2
[0036] (1) Take by weighing 800g boehmite, 300g bentonite, 160g basic calcium phosphate, pulverize boehmite in a pulverizer, cross a 500 mesh sieve, then fully mix boehmite, bentonite, basic calcium phosphate, Stir with a high-speed mixer for 60 minutes to obtain mixture A;
[0037] (2) Weigh 600g octabromobisphenol S ether, 160g nano-calcium silicate, and 800g mixture A, add octabromobisphenol S ether and nano-calcium silicate to step (1) mixture A, fully stir and mix for 40min, Cool to room temperature to obtain low VOC flame retardant composite filler P2.
[0038] Wherein the temperature of the high-speed mixer in the step (1) is 90° C., and the rotating speed is 320 r / min.
PUM
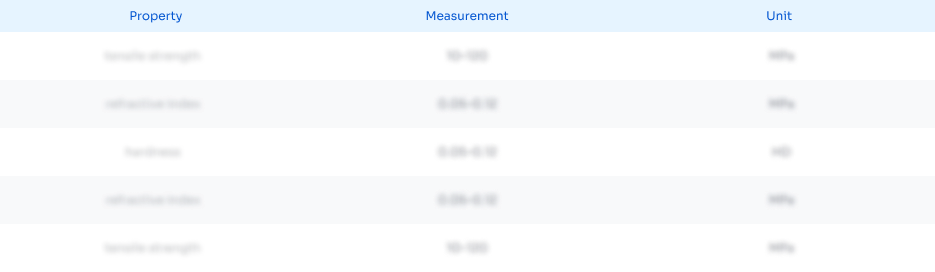
Abstract
Description
Claims
Application Information

- R&D
- Intellectual Property
- Life Sciences
- Materials
- Tech Scout
- Unparalleled Data Quality
- Higher Quality Content
- 60% Fewer Hallucinations
Browse by: Latest US Patents, China's latest patents, Technical Efficacy Thesaurus, Application Domain, Technology Topic, Popular Technical Reports.
© 2025 PatSnap. All rights reserved.Legal|Privacy policy|Modern Slavery Act Transparency Statement|Sitemap|About US| Contact US: help@patsnap.com