Ultra-high performance concrete slurry, ultra-high performance concrete and preparation method thereof
An ultra-high performance, concrete slurry technology, applied in ultra-high-performance concrete and its preparation, ultra-high-performance concrete slurry field, can solve the problems of limited use range, difficult to achieve curing conditions, and complex construction technology of ultra-high-performance concrete. , to achieve the effects of excellent mechanical properties, convenient maintenance methods, and simple production processes
- Summary
- Abstract
- Description
- Claims
- Application Information
AI Technical Summary
Problems solved by technology
Method used
Image
Examples
Embodiment 1
[0047] The embodiment of the present invention provides the first ultra-high performance concrete, and its preparation method includes the following steps:
[0048] (1) According to the weight compounding relationship in Table 1, add cement 674.21kg, microsilica fume 168.55kg, quartz powder 202.26kg, silica sand 985.5kg (including coarse particle size silica sand 703.93kg, medium particle size silica sand 201.12kg) into the forced mixer kg and fine particle size silica sand 80.45kg), stirred for 5 minutes;
[0049] (2) Then, while stirring, add 6.74kg of nano silicon dioxide, 188.10.kg of water and 41.8kg of water reducer solution (10.45kg of water reducer and 31.35kg of water are mixed and prepared), and stir for 4 minutes;
[0050] (3) Add 196.25 kg of steel fiber at last, stir for 8 minutes, and obtain ultra-high performance concrete slurry;
[0051] (4) Pour the ultra-high-performance concrete slurry into the mold three times, pouring one-third of the volume each time, us...
Embodiment 2
[0053] The embodiment of the present invention provides the second ultra-high performance concrete, and its preparation method includes the following steps:
[0054] (1) According to the weight compounding relationship in Table 1, add cement 674.21kg, microsilica fume 168.55kg, quartz powder 202.26kg, silica sand 985.5kg (including coarse particle size silica sand 703.93kg, medium particle size silica sand 201.12kg) into the forced mixer kg and fine particle size silica sand 80.45kg), stirred for 5 minutes;
[0055] (2) Then, while stirring, add 13.48kg of nano silicon dioxide, 188.10.kg of water and 41.8kg of water reducer solution (10.45kg of water reducer and 31.35kg of water are mixed and prepared), and stir for 4 minutes;
[0056] (3) Add 196.25 kg of steel fiber at last, stir for 8 minutes, and obtain ultra-high performance concrete slurry;
[0057] (4) Pour the ultra-high-performance concrete slurry into the mold three times, pouring one-third of the volume each time, ...
Embodiment 3
[0059] The embodiment of the present invention provides the third ultra-high performance concrete, and its preparation method includes the following steps:
[0060] (1) According to the weight compounding relationship in Table 1, add cement 674.21kg, microsilica fume 168.55kg, quartz powder 202.26kg, silica sand 985.5kg (including coarse particle size silica sand 703.93kg, medium particle size silica sand 201.12kg) into the forced mixer kg and fine particle size silica sand 80.45kg), stirred for 5 minutes;
[0061] (2) Then, while stirring, add 20.23kg of nano silicon dioxide, 188.10.kg of water and 41.8kg of water reducer solution (10.45kg of water reducer and 31.35kg of water are mixed and prepared), and stir for 4 minutes;
[0062] (3) Add 196.25 kg of steel fiber at last, stir for 8 minutes, and obtain ultra-high performance concrete slurry;
[0063] (4) Pour the ultra-high-performance concrete slurry into the mold three times, pouring one-third of the volume each time, u...
PUM
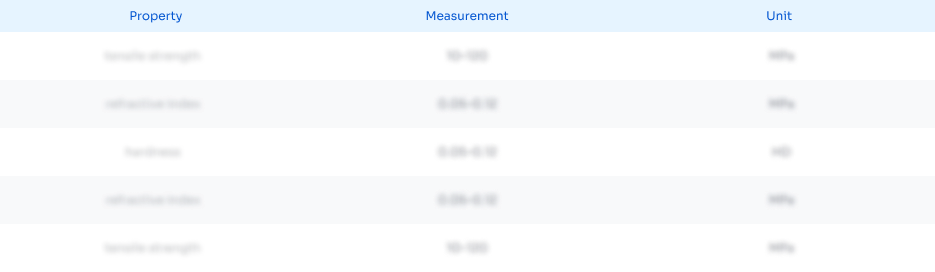
Abstract
Description
Claims
Application Information

- R&D
- Intellectual Property
- Life Sciences
- Materials
- Tech Scout
- Unparalleled Data Quality
- Higher Quality Content
- 60% Fewer Hallucinations
Browse by: Latest US Patents, China's latest patents, Technical Efficacy Thesaurus, Application Domain, Technology Topic, Popular Technical Reports.
© 2025 PatSnap. All rights reserved.Legal|Privacy policy|Modern Slavery Act Transparency Statement|Sitemap|About US| Contact US: help@patsnap.com