Special impregnating agent for electronic fabric warps and preparation process of impregnating agent
A preparation process and technology of electronic cloth, which is applied in the field of glass fiber, can solve the problems of affecting the use effect and high residue of wetting agent on the cloth surface, and achieve the effects of saving production cost, eliminating the twisting process, and good social and economic benefits
- Summary
- Abstract
- Description
- Claims
- Application Information
AI Technical Summary
Problems solved by technology
Method used
Examples
Embodiment 1
[0025] Prepare materials in proportion: No. 58 paraffin 1.9%, No. 15 engine oil 1.8%, emulsifier Pingping 0.9%, alkyl imidazoline lubricant 0.15%, color fixing agent 4.8%, vegetable oleic acid 1.2%, dibutyl ester 0.45%, Water-soluble polyester resin 4%, the balance is water;
[0026] Preparation Process:
[0027] 1) Heat No. 58 paraffin wax, engine oil, dibutyl ester, vegetable oleic acid, alkyl imidazoline lubricant, and water-soluble unsaturated polyester resin weighed in proportion to 85°C to melt to obtain a molten material;
[0028] 2) Heat the color fixing agent to 85°C;
[0029] 3) Add the heated color fixing agent into the molten material in step 1) and start stirring to obtain the mixed raw material;
[0030] 4) Then add hot water at 86°C until the mixed raw materials become a paste, and then add hot water at 65°C. The total amount of water added in this step is 1 / 3 of the formula amount;
[0031] 5) After stirring for 30 minutes, add epoxy resin diluted with hot w...
Embodiment 2
[0033] Prepare materials in proportion: No. 58 paraffin wax 1.9%, No. 10 engine oil 1.6%, emulsifier Pingpingjia 0.95%, alkyl imidazoline lubricant 0.13%, color fixing agent 4.7%, vegetable oleic acid 1.1%, dibutyl ester 0.48%, Water-soluble polyester resin 3.5%, the balance is water;
[0034] Preparation Process:
[0035] 1) Heat No. 58 paraffin wax, engine oil, dibutyl ester, vegetable oleic acid, alkyl imidazoline lubricant, and water-soluble unsaturated polyester resin weighed in proportion to 83°C to melt to obtain a molten material;
[0036] 2) Heat the color fixing agent to 82°C;
[0037] 3) Add the heated color fixing agent into the molten material in step 1) and start stirring to obtain the mixed raw material;
[0038] 4) Then add hot water at 85°C until the mixed raw materials are in a paste form, and then add hot water at 60°C. The total amount of water added in this step is 1 / 2 of the formula amount;
[0039] 5) After stirring for 32 minutes, add epoxy resin dil...
Embodiment 3
[0041] Raw materials prepared in proportion: No. 58 paraffin wax 1.9%, No. 7 engine oil ~ No. 15 engine oil 1.8%, emulsifier Pingpingjia 0.98%, alkyl imidazoline lubricant 0.18%, color fixing agent 4.8%, vegetable oleic acid 1.4%, dibutylene 0.42% ester, 4.5% water-soluble polyester resin, and water as the balance;
[0042] Preparation Process:
[0043] 1) Heat No. 58 paraffin wax, engine oil, dibutyl ester, vegetable oleic acid, alkyl imidazoline lubricant, and water-soluble unsaturated polyester resin weighed in proportion to 85°C to melt to obtain a molten material;
[0044] 2) Heat the color fixing agent to 88°C;
[0045] 3) Add the heated color fixing agent into the molten material in step 1) and start stirring to obtain the mixed raw material;
[0046] 4) Then add hot water at 87°C until the mixed raw materials are in paste form, and then add hot water at 70°C. The total amount of water added in this step is 1 / 3 of the formula amount;
[0047] 5) After stirring for 29...
PUM
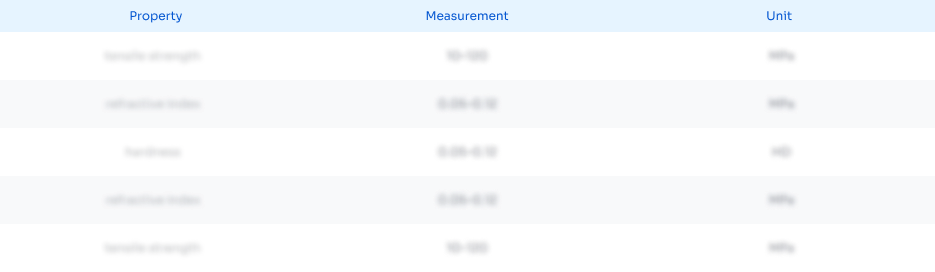
Abstract
Description
Claims
Application Information

- Generate Ideas
- Intellectual Property
- Life Sciences
- Materials
- Tech Scout
- Unparalleled Data Quality
- Higher Quality Content
- 60% Fewer Hallucinations
Browse by: Latest US Patents, China's latest patents, Technical Efficacy Thesaurus, Application Domain, Technology Topic, Popular Technical Reports.
© 2025 PatSnap. All rights reserved.Legal|Privacy policy|Modern Slavery Act Transparency Statement|Sitemap|About US| Contact US: help@patsnap.com