Printing glazing oil and preparation method thereof
A technology of varnish and ink, applied in coating and other directions, can solve the problems of poor friction resistance and slow drying speed of varnish, and achieve the effects of good leveling, high bearing capacity and shortened induction period.
- Summary
- Abstract
- Description
- Claims
- Application Information
AI Technical Summary
Problems solved by technology
Method used
Image
Examples
preparation example Construction
[0023] The preparation method of glazing oil base material is:
[0024] (1) In parts by mass, take 2~7 parts of methyl methacrylate, 4~6 parts of 2-ethylhexyl acrylate, 1~3 parts of methylol acrylamide, 8~10 parts of styrene, 3~5 parts of itaconic acid, 3~6 parts of methacrylate, 0.5~0.8 parts of azobisisobutyronitrile, stir and mix for 20~30min to obtain a mixture, take ethyl acetate at a mass ratio of 2~5:1~ 3. Add N-methylpyrrolidone and mix to obtain a mixed solution. Take the mixture and add it to the mixed solution according to the mass ratio of 1~5:10~20, heat up to 50~60°C and stir for 30~40 minutes, add dropwise 1~3% of the mixture Azobisisobutyronitrile and 2-mercaptoethanol with a mixing mass of 2~5% were stirred and mixed at 80~85°C for 40~60 minutes to obtain a stirred mixture, and the stirred mixture was added to the deionized mixture at a mass ratio of 2~5:8~10 water, stirred and mixed for 30~40min to obtain mixture a;
[0025] (2) Take the mixture a and add N...
Embodiment 1
[0035] The preparation method of glazing oil base material is:
[0036] (1) In parts by mass, take 2 parts of methyl methacrylate, 4 parts of 2-ethylhexyl acrylate, 1 part of methylol acrylamide, 8 parts of styrene, 3 parts of itaconic acid, 3 parts Methacrylate and 0.5 parts of azobisisobutyronitrile were stirred and mixed for 20 minutes to obtain a mixture, and ethyl acetate was mixed with N-methylpyrrolidone at a mass ratio of 2:1 to obtain a mixed solution, and the mixture was obtained at a mass ratio of 1: 10 Add the mixed solution, heat up to 50°C and stir for 30 minutes, add dropwise azobisisobutyronitrile of 1% by weight of the mixture and 2-mercaptoethanol of 2% by weight of the mixture, stir and mix for 40 minutes at 80°C to obtain a stirred mixture, take the stirring Add deionized water to the mixture at a mass ratio of 2:8, stir and mix for 30 minutes to obtain mixture a;
[0037] (2) Take the mixture a and add N-methyldiethanolamine and styrene according to the m...
Embodiment 2
[0047] The preparation method of glazing oil base material is:
[0048] (1) In parts by mass, take 7 parts of methyl methacrylate, 6 parts of 2-ethylhexyl acrylate, 3 parts of methylol acrylamide, 10 parts of styrene, 5 parts of itaconic acid, 6 parts Methacrylate and 0.8 parts of azobisisobutyronitrile were stirred and mixed for 30 minutes to obtain a mixture, and ethyl acetate was mixed with N-methylpyrrolidone at a mass ratio of 5:3 to obtain a mixed solution, and the mixture was obtained at a mass ratio of 5: 20 Add the mixed solution, heat up to 60°C and stir for 40 minutes, add 3% azobisisobutyronitrile and 5% 2-mercaptoethanol dropwise, and stir and mix at 85°C for 60 minutes to obtain a stirred mixture. Add deionized water to the mixture at a mass ratio of 5:10, stir and mix for 40 minutes to obtain mixture a;
[0049] (2) Take the mixture a and add N-methyldiethanolamine and styrene at a mass ratio of 150:5:10, stir and mix at 35°C for 50 minutes to obtain the stirre...
PUM
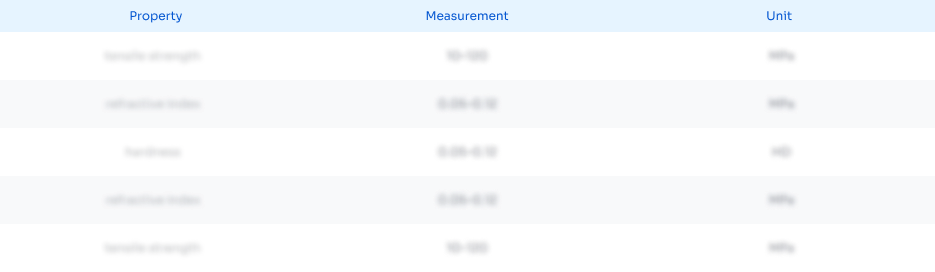
Abstract
Description
Claims
Application Information

- Generate Ideas
- Intellectual Property
- Life Sciences
- Materials
- Tech Scout
- Unparalleled Data Quality
- Higher Quality Content
- 60% Fewer Hallucinations
Browse by: Latest US Patents, China's latest patents, Technical Efficacy Thesaurus, Application Domain, Technology Topic, Popular Technical Reports.
© 2025 PatSnap. All rights reserved.Legal|Privacy policy|Modern Slavery Act Transparency Statement|Sitemap|About US| Contact US: help@patsnap.com