Silicomanganese furnace tail gas isothermal and sulfur-free transformation technology and system
An isothermal shift and tail gas technology, applied in the field of warm sulfur-free shift process and system, can solve the problems of long catalyst operation period, easy partial sintering of driving force, etc.
- Summary
- Abstract
- Description
- Claims
- Application Information
AI Technical Summary
Problems solved by technology
Method used
Image
Examples
Embodiment 1
[0078] Refer to attached figure 1 , the conversion system in this embodiment includes a pretreatment device 8, the input end of the pretreatment device is used to directly connect with the exhaust gas generating device to receive the tail gas produced by the tail gas generating device, and to process the tail gas dust removal;
[0079] The fine desulfurization device 1, the input end of the fine desulfurization device 1 is directly connected with the output end of the pretreatment device 8, and is used to directly receive the raw material gas treated by the pretreatment device 8 and desulfurize it.
[0080] Preferably, the fine desulfurization device is used to remove the total sulfur in the tail gas to below 0.1 ppm.
[0081] Preferably, the conversion system also includes:
[0082] Purification furnace 3, the input end of the purification furnace is connected to the output end of the fine desulfurization device, used to receive the tail gas from the output end of the desul...
Embodiment 2
[0105] This embodiment provides an isothermal sulfur-free transformation process for silicomanganese furnace tail gas, which includes the following steps:
[0106] (1) directly desulfurize the tail gas after dedusting and pressurization;
[0107] (2) Dephosphorize, dechlorinate, defluorinate and deoxygenate the tail gas at the set temperature;
[0108] (3) adjust the steam-gas ratio in the tail gas to carry out the conversion reaction;
[0109] Preferably, step (1) the tail gas of the silicomanganese furnace is pressurized to 0.8Mpag.
[0110] Preferably, step (1) the tail gas of the silicomanganese furnace is pressurized to 2.7Mpag.
[0111] Preferably, step (1) the tail gas of the silicomanganese furnace is pressurized to 3.0Mpag.
[0112] Different pressures can be adopted according to different requirements of transformation reactions. Generally, the driving force of high pressure reaction is relatively large, and the volume of equipment is small, which is beneficial t...
PUM
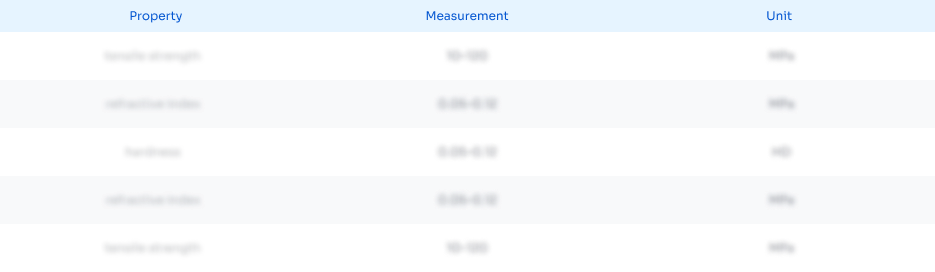
Abstract
Description
Claims
Application Information

- Generate Ideas
- Intellectual Property
- Life Sciences
- Materials
- Tech Scout
- Unparalleled Data Quality
- Higher Quality Content
- 60% Fewer Hallucinations
Browse by: Latest US Patents, China's latest patents, Technical Efficacy Thesaurus, Application Domain, Technology Topic, Popular Technical Reports.
© 2025 PatSnap. All rights reserved.Legal|Privacy policy|Modern Slavery Act Transparency Statement|Sitemap|About US| Contact US: help@patsnap.com