A three-dimensional modeling method of diffractive optical element based on matrix transformation
A technology for diffractive optical elements and three-dimensional modeling, which is applied in the field of three-dimensional modeling of diffractive optical elements based on matrix transformation, and can solve the problems that the surface of diffractive optical elements is difficult to represent, the processing method is cumbersome, and the workload of analysis and calculation is large.
- Summary
- Abstract
- Description
- Claims
- Application Information
AI Technical Summary
Problems solved by technology
Method used
Image
Examples
Embodiment 1
[0029] It is designed to make the modeling process of aperiodic continuous relief diffractive optical elements fast, accurate and efficient. Broaden the way for micro-nano processing of diffractive optical elements, including traditional processing methods, such as diamond cutting, and other processing methods, such as micro-nano 3D printing.
[0030] This implementation example proposes a modeling method for diffractive optical elements based on matrix transformation.
[0031] The phase matrix is designed through the optimization algorithm implemented by MATLAB, the corresponding relationship between the point cloud and the phase matrix data is established, and the point cloud file that can be directly read by Pro / E is generated, and the high-precision model is generated from the obtained point cloud file using the method of reverse engineering.
[0032] This method mainly adopts the idea of combining data conversion and reverse engineering, and consists of four main modu...
PUM
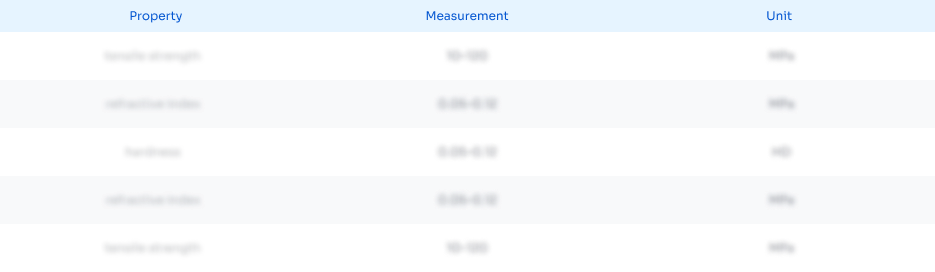
Abstract
Description
Claims
Application Information

- R&D
- Intellectual Property
- Life Sciences
- Materials
- Tech Scout
- Unparalleled Data Quality
- Higher Quality Content
- 60% Fewer Hallucinations
Browse by: Latest US Patents, China's latest patents, Technical Efficacy Thesaurus, Application Domain, Technology Topic, Popular Technical Reports.
© 2025 PatSnap. All rights reserved.Legal|Privacy policy|Modern Slavery Act Transparency Statement|Sitemap|About US| Contact US: help@patsnap.com