Dipping solution used for producing dipped polyester canvas by single bath method and preparation method thereof
A technology of dipping liquid and dipping glue, which is applied in the direction of fiber type, textile and paper making, fiber processing, etc. The effect of increasing production efficiency and improving strength
- Summary
- Abstract
- Description
- Claims
- Application Information
AI Technical Summary
Problems solved by technology
Method used
Examples
Embodiment 1
[0018] This embodiment provides a dipping solution for producing dipped polyester canvas by a single-bath method. The formula mass parts of the dipping solution are as follows: 158 parts of soft water, 12 parts of resorcinol, 13 parts of formaldehyde, and 18 parts of p-chlorophenol 300 parts, 300 parts of styrene-butadiene latex, 12 parts of ammonia water, 18 parts of isocyanate solution, and 0.65 parts of sodium hydroxide.
[0019] This embodiment also provides a method for preparing a dipping solution for producing dipped polyester canvas by a single-bath method, and the steps of the preparation method are as follows:
[0020] Step 1: Add soft water into the reaction kettle and stir;
[0021] Step 2: add resorcinol in the reactor and stir;
[0022] Step 3: Add formaldehyde solution and keep stirring;
[0023] Step 4: judge whether the above solution has completed the reaction;
[0024] Step five: add p-chlorophenol to the solution that has completed the reaction, and keep...
Embodiment 2
[0028] This embodiment provides a dipping solution for producing dipped polyester canvas by a single-bath method. The formula mass parts of the dipping solution are as follows: 140 parts of soft water, 10 parts of resorcinol, 13 parts of formaldehyde, and 15 parts of p-chlorophenol 250 parts, 250 parts of styrene-butadiene latex, 10 parts of ammonia water, 18 parts of isocyanate solution, and 0.3 parts of sodium hydroxide.
[0029] The preparation method of this embodiment is consistent with that of Embodiment 1.
Embodiment 3
[0031] This embodiment provides a dipping solution for producing dipped polyester canvas by a single-bath method. The formula mass parts of the dipping solution are as follows: 170 parts of soft water, 12 parts of resorcinol, 15 parts of formaldehyde, and 20 parts of p-chlorophenol 350 parts, 350 parts of styrene-butadiene latex, 15 parts of ammonia water, 20 parts of isocyanate solution, 1 part of sodium hydroxide.
[0032] The preparation method of this embodiment is consistent with that of Embodiment 1.
PUM
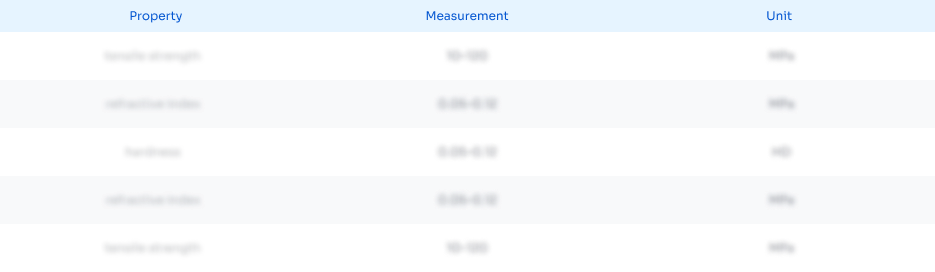
Abstract
Description
Claims
Application Information

- R&D
- Intellectual Property
- Life Sciences
- Materials
- Tech Scout
- Unparalleled Data Quality
- Higher Quality Content
- 60% Fewer Hallucinations
Browse by: Latest US Patents, China's latest patents, Technical Efficacy Thesaurus, Application Domain, Technology Topic, Popular Technical Reports.
© 2025 PatSnap. All rights reserved.Legal|Privacy policy|Modern Slavery Act Transparency Statement|Sitemap|About US| Contact US: help@patsnap.com