A control system and method for laser radar galvanometer servo motor
A technology of servo motor and laser radar, which is applied in general control system, control/adjustment system, computer control, etc., can solve the problems of no advantages in speed and precision indicators, complex neural network control, and low speed indicators, etc., and reach the target area range The effect of wide, fast response and large scanning angle
- Summary
- Abstract
- Description
- Claims
- Application Information
AI Technical Summary
Problems solved by technology
Method used
Image
Examples
Embodiment 1
[0062]This embodiment is directed to the control system of the laser radar spray hammer motor, including:
[0063]1) Select high-frequency laser front end to generate high-frequency lasers, using high sensitivity detectors to receive laser ranging echo;
[0064]2) Use the scanning gammery to change the laser light path to periodically scan the designated area;
[0065]3) Pass the resulting laser beam position and target distance information to the host computer by driving the control digital module;
[0066]4) The upper machine draws the point cloud image of the specified area through three-dimensional reconstruction software.
[0067]The servo drive control system consists of a driving control digital module and a three-ring control analog module, and the drive control digital module consists of ARM, FPGA. The drive control digital module has a function of generating a drive signal, a processing feedback signal, a state of determining a system, and selecting a control policy.
[0068]figure 1 It is ...
PUM
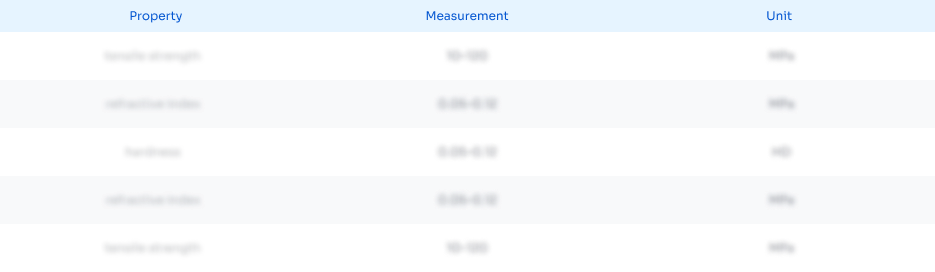
Abstract
Description
Claims
Application Information

- R&D
- Intellectual Property
- Life Sciences
- Materials
- Tech Scout
- Unparalleled Data Quality
- Higher Quality Content
- 60% Fewer Hallucinations
Browse by: Latest US Patents, China's latest patents, Technical Efficacy Thesaurus, Application Domain, Technology Topic, Popular Technical Reports.
© 2025 PatSnap. All rights reserved.Legal|Privacy policy|Modern Slavery Act Transparency Statement|Sitemap|About US| Contact US: help@patsnap.com