Printing and dyeing technology for pure cotton dyed twill fabric
A printing and dyeing process, twill technology, applied in dyeing, singeing, dry-cleaning fiber products, etc., to achieve the effect of improving humanized design
- Summary
- Abstract
- Description
- Claims
- Application Information
AI Technical Summary
Problems solved by technology
Method used
Image
Examples
Embodiment 1
[0029] A printing and dyeing process for pure cotton twill dyed cloth, characterized in that it comprises the following eight steps:
[0030] Step 1: Raw cloth preparation;
[0031] Step 2: singeing process;
[0032] Step 3: desizing process;
[0033] Step 4: Cooking process;
[0034] Step five: bleaching process;
[0035] Step six: dyeing process;
[0036] Step 7: Mercerizing process;
[0037] Step 8: Finishing process.
[0038] Said raw cloth preparation, raw cloth preparation includes raw cloth inspection, cloth turning (batch, sub-box, printing) and seam head, the purpose of raw cloth inspection is to check the quality of gray cloth, find that problems can be solved in time, inspection content includes physical Indicators and appearance defects, the former includes the length, width, weight, warp and weft yarn density and density, strength, etc. of the original fabric, and the latter such as spinning defects, weaving defects, various spots and damage, etc. About 10%...
Embodiment 2
[0047] A kind of pure cotton twill dyeing cloth printing and dyeing process that embodiment 1 obtains is illustrated, as follows:
[0048] With the advancement of technology, there will continue to be new finishing processes and materials, color fastness and color fastness are the most important indicators of dyed fabrics. It is called color fastness. After dyeing and printing, textiles sometimes have to go through other processes, such as milling of wool fabrics, heat setting of synthetic fiber textiles, etc.; in the process of wearing, they must be exposed to the atmosphere, sweat stains, and withstand washing and friction. External effects such as ironing and ironing can cause different degrees of fading and discoloration of printed and dyed textiles. The processes that affect the color fastness of printed and dyed textiles are mainly milling, carbonization, chlorine bleaching, sublimation, etc. Dyes or pigments on textiles The color fastness of various materials is related...
PUM
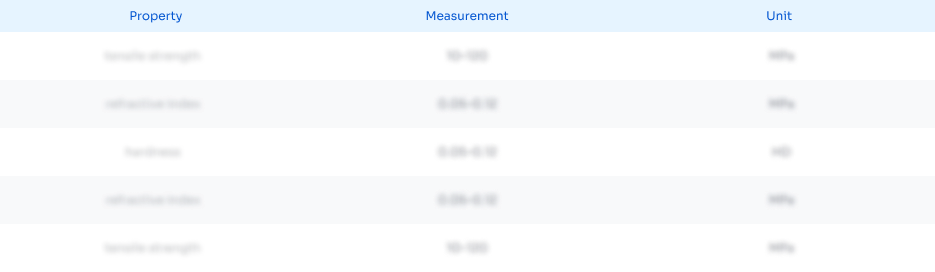
Abstract
Description
Claims
Application Information

- R&D
- Intellectual Property
- Life Sciences
- Materials
- Tech Scout
- Unparalleled Data Quality
- Higher Quality Content
- 60% Fewer Hallucinations
Browse by: Latest US Patents, China's latest patents, Technical Efficacy Thesaurus, Application Domain, Technology Topic, Popular Technical Reports.
© 2025 PatSnap. All rights reserved.Legal|Privacy policy|Modern Slavery Act Transparency Statement|Sitemap|About US| Contact US: help@patsnap.com