Large-damping efficiently-cooling radial passive permanent magnet bearing structure
A permanent magnetic bearing, high-efficiency technology, applied in the direction of bearings, bearing components, shafts and bearings, etc., can solve the problems of large power consumption, large volume, and reducing the critical speed of the rotor
- Summary
- Abstract
- Description
- Claims
- Application Information
AI Technical Summary
Problems solved by technology
Method used
Image
Examples
Embodiment Construction
[0015] The present invention will be described in further detail below in conjunction with the accompanying drawings.
[0016] refer to figure 1 and figure 2 , a radial passive permanent magnet bearing structure with large damping and efficient cooling, including a stator permanent magnet 2 transitionally fitted with a stator frame 1, a sliding bearing 3 is arranged in the cavity of the stator permanent magnet 2, and the outer side of the sliding bearing 3 is connected to the stator permanent magnet 2 Adopt clearance fit, the two sides of the stator permanent magnet 2 are respectively bonded with the left plug 4a of the stator permanent magnet and the right plug 4b of the stator permanent magnet, and a stator-rotor gap 5 is provided between the inner side of the sliding bearing 3 and the outer side of the rotor sleeve 7 , there are oil inlet 6a and oil outlet 6b on both sides of the stator-rotor gap 5, lubricating oil enters the stator-rotor gap 5 from the oil inlet 6a, and ...
PUM
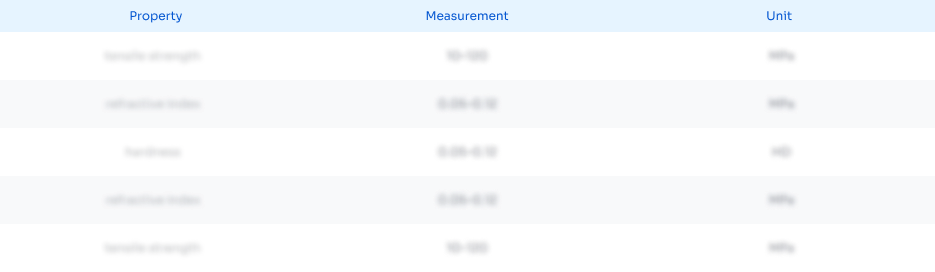
Abstract
Description
Claims
Application Information

- R&D
- Intellectual Property
- Life Sciences
- Materials
- Tech Scout
- Unparalleled Data Quality
- Higher Quality Content
- 60% Fewer Hallucinations
Browse by: Latest US Patents, China's latest patents, Technical Efficacy Thesaurus, Application Domain, Technology Topic, Popular Technical Reports.
© 2025 PatSnap. All rights reserved.Legal|Privacy policy|Modern Slavery Act Transparency Statement|Sitemap|About US| Contact US: help@patsnap.com