Gravure printing process for flexible packaging
A gravure printing process and flexible packaging technology, applied in the printing field, can solve problems such as peeling, ink stickiness, and finished product defects, and achieve the effects of uniform particle size, improved coloring effect, and moderate viscosity
- Summary
- Abstract
- Description
- Claims
- Application Information
AI Technical Summary
Problems solved by technology
Method used
Image
Examples
Embodiment 1
[0040] A gravure printing process for flexible packaging
[0041] Step 1: Design manuscript and manuscript review
[0042] Design the design manuscript of flexible packaging according to the needs of flexible packaging products, and then review the design manuscript to confirm that it is correct;
[0043] Step 2: Make a gravure printing plate
[0044] Make a gravure printing plate according to the size parameters of the flexible packaging on the design manuscript after review, and the surface roughness of the gravure printing plate is Ra0.8;
[0045] Step 3: Prepare materials
[0046] Select the flexible packaging substrate according to the typesetting on the design manuscript, the material structure and the relevant parameters of the thickness of the finished product;
[0047] Step 4: Prepare Ink
[0048] In the step four, first add 40 parts by mass of polyamide resin and 12 parts by mass of nitrocellulose into the stirred tank, the temperature in the stirred tank is rais...
Embodiment 2
[0062] A gravure printing process for flexible packaging
[0063] Step 1: Design manuscript and manuscript review
[0064] Design the design manuscript of flexible packaging according to the needs of flexible packaging products, and then review the design manuscript to confirm that it is correct;
[0065] Step 2: Make a gravure printing plate
[0066] Make a gravure printing plate according to the size parameters of the flexible packaging on the design manuscript after review, and the surface roughness of the gravure printing plate is Ra0.8;
[0067] Step 3: Prepare materials
[0068] Select the flexible packaging substrate according to the typesetting on the design manuscript, the material structure and the relevant parameters of the thickness of the finished product;
[0069] Step 4: Prepare Ink
[0070] In the step 4, 45 parts by mass of polyamide resin and nitrocellulose of 14 parts by mass are first added to the stirred tank, the temperature in the stirred tank is rai...
Embodiment 3
[0084] A gravure printing process for flexible packaging
[0085] Step 1: Design manuscript and manuscript review
[0086] Design the design manuscript of flexible packaging according to the needs of flexible packaging products, and then review the design manuscript to confirm that it is correct;
[0087] Step 2: Make a gravure printing plate
[0088] Make a gravure printing plate according to the size parameters of the flexible packaging on the design manuscript after review, and the surface roughness of the gravure printing plate is Ra0.8;
[0089] Step 3: Prepare materials
[0090] Select the flexible packaging substrate according to the typesetting on the design manuscript, the material structure and the relevant parameters of the thickness of the finished product;
[0091] Step 4: Prepare Ink
[0092] In the step 4, 50 parts by mass of polyamide resin and nitrocellulose of 15 parts by mass are first added to the stirred tank, the temperature in the stirred tank is rai...
PUM
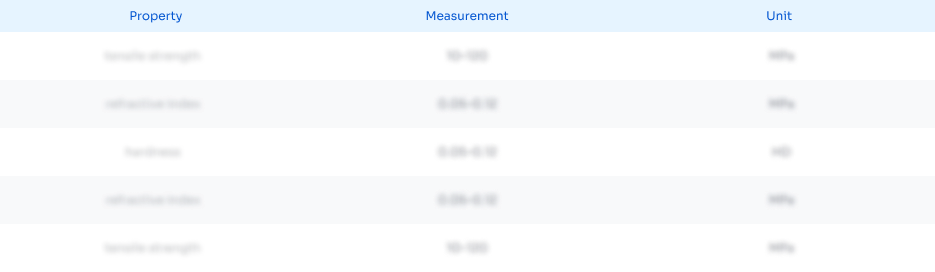
Abstract
Description
Claims
Application Information

- R&D
- Intellectual Property
- Life Sciences
- Materials
- Tech Scout
- Unparalleled Data Quality
- Higher Quality Content
- 60% Fewer Hallucinations
Browse by: Latest US Patents, China's latest patents, Technical Efficacy Thesaurus, Application Domain, Technology Topic, Popular Technical Reports.
© 2025 PatSnap. All rights reserved.Legal|Privacy policy|Modern Slavery Act Transparency Statement|Sitemap|About US| Contact US: help@patsnap.com