Method for 3D printing of bicomponent composite material with skin-core structure
A skin-core structure and composite material technology, applied in 3D object support structures, additive processing, coating devices, etc., can solve the problems of easy separation and uneven distribution of materials, and achieve difficult separation, rich varieties, and product performance. excellent effect
- Summary
- Abstract
- Description
- Claims
- Application Information
AI Technical Summary
Problems solved by technology
Method used
Examples
Embodiment 1
[0023] A method for 3D printing a skin-core structure two-component composite material. The 3D printer is mainly composed of a silo I, a silo II, a screw extruder I, a screw extruder II, a metering pump I, a metering pump II, a distribution plate, Composed of nozzles and multiple melt pipes, silo I and silo II are connected to screw extruder I and screw extruder II respectively, and screw extruder I and screw extruder II are respectively connected to metering pumps through melt pipes I is connected to the metering pump II, the metering pump I and the metering pump II are connected to the same distribution plate, and the distribution plate is connected to the nozzle, the specific steps are as follows:
[0024] (1) Polycaprolactone powder and nylon particles are melted in screw extruder I and screw extruder II respectively from silo I and silo II; Dry in a vacuum oven with a temperature of 60°C and a vacuum of 60% for 10 hours; nylon is dried in a vacuum oven with a temperature ...
Embodiment 2
[0028] A method for 3D printing a two-component composite material with a skin-core structure, the structure of the 3D printer is consistent with that of Example 1, and the specific steps are as follows:
[0029] (1) Block polylactic acid and ABS particles are melted in screw extruder I and screw extruder II respectively from silo I and silo II; wherein, polylactic acid is heated at a temperature of 110 ℃ and a vacuum of 70% in a vacuum drying oven for 8 hours; ABS was dried for 7 hours in a vacuum drying oven with a temperature of 130 °C and a vacuum of 95% before entering the silo II, and the screw extruder I The internal temperature is 180°C and the pressure is 25.0MPa. The internal temperature of the screw extruder II is 100°C and the pressure is 45MPa. The silo I and silo II are protected by nitrogen;
[0030] (2) transported by the melt pipeline to metering pump I and metering pump II;
[0031] (3) After being metered into the same distribution plate by the metering pum...
Embodiment 3
[0033] A method for 3D printing a two-component composite material with a skin-core structure, the structure of the 3D printer is consistent with that of Example 1, and the specific steps are as follows:
[0034] (1) Nylon 6 powder and polycarbonate particles are melted in the screw extruder I and the screw extruder II from the silo I and the silo II respectively; Dry in a vacuum oven at 150°C and a vacuum of 50% for 11 hours; polycarbonate is dried in a vacuum oven at a temperature of 110°C and a vacuum of 90% for 12 hours before entering the silo II. The temperature inside the extruder I is 250°C and the pressure is 40MPa, the temperature inside the screw extruder II is 220°C and the pressure is 15.0MPa, and the bin I and bin II are protected by nitrogen;
[0035] (2) transported by the melt pipeline to metering pump I and metering pump II;
[0036] (3) After being metered into the same distribution plate by the metering pump, the distribution plate is distributed to the ou...
PUM
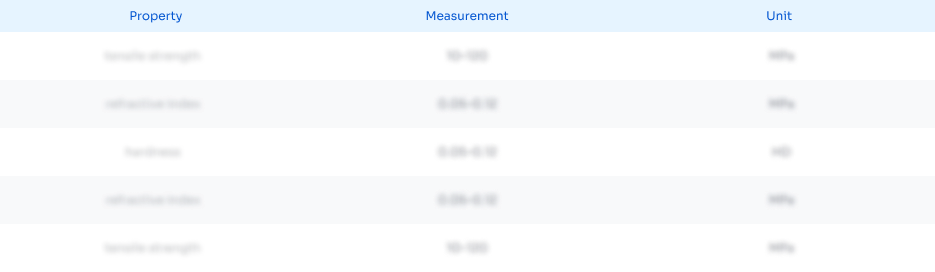
Abstract
Description
Claims
Application Information

- R&D
- Intellectual Property
- Life Sciences
- Materials
- Tech Scout
- Unparalleled Data Quality
- Higher Quality Content
- 60% Fewer Hallucinations
Browse by: Latest US Patents, China's latest patents, Technical Efficacy Thesaurus, Application Domain, Technology Topic, Popular Technical Reports.
© 2025 PatSnap. All rights reserved.Legal|Privacy policy|Modern Slavery Act Transparency Statement|Sitemap|About US| Contact US: help@patsnap.com