Aircraft floor slide track test device and application method
The technology of a test device and slide rail is applied in the direction of measuring device, application of stable tension/pressure test material strength, instruments, etc., which can solve the problems such as the lack of aircraft floor slide rail test devices and methods, and achieve strong practicability and eliminate Effect of torque influence
- Summary
- Abstract
- Description
- Claims
- Application Information
AI Technical Summary
Problems solved by technology
Method used
Image
Examples
Embodiment 1
[0030] see Figure 1-8 , in an embodiment of the present invention, an aircraft floor slide rail test device includes a fixture A1 and a fixture B2, and the fixture A1 and the fixture B2 cooperate to clamp and fix the slide rail 3, and the bottom surfaces of the fixture A1 and the fixture B2 and the slide rail 3's inner edge contacts.
[0031] The clamping surface of the fixture A1 (the contact surface with the slide rail 3) is processed according to the shape modification of the web plate of the aircraft slide rail 3 and the inner edge of the slide rail 3, and a fastening bolt 4 passes through the hole A; the clamp B2 The clamping surface (the surface in contact with the slide rail 3) is modified and processed according to the shape of the aircraft slide rail 3 web and the inner edge of the slide rail 3, and a fastening bolt 4 passes through the hole B; the clamp A1 and the clamp B2 pass through The fastening bolts 4 are connected and fixed through the corresponding holes A ...
Embodiment 2
[0044] refer to Figure 9The difference between this embodiment and Embodiment 1 is that it also includes an actuator 9 for applying a vertical load to the loading joint 7, one end of the actuator 9 is hinged and fixed, and the other end of the actuator 9 passes through the sensor C15 is connected with the loading joint 7 to realize multi-directional combined loading on the basis of the original single-directional loading.
[0045] The aircraft floor slide rail test device has designed the aircraft slide rail 3 clamping structure, which is used to simulate the constraints of the aircraft floor slide rail 3 in actual use, and has designed a special loading joint 7, a ferrule 8 and an auxiliary loading structure for use in The aircraft slide rail 3 is actually loaded, and the equipment connection method and control strategy are proposed, which can realize the application of the test force while eliminating the influence of the moment, and can conveniently realize single-directio...
PUM
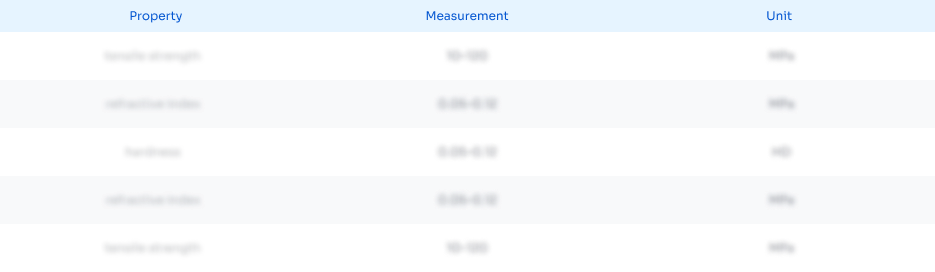
Abstract
Description
Claims
Application Information

- Generate Ideas
- Intellectual Property
- Life Sciences
- Materials
- Tech Scout
- Unparalleled Data Quality
- Higher Quality Content
- 60% Fewer Hallucinations
Browse by: Latest US Patents, China's latest patents, Technical Efficacy Thesaurus, Application Domain, Technology Topic, Popular Technical Reports.
© 2025 PatSnap. All rights reserved.Legal|Privacy policy|Modern Slavery Act Transparency Statement|Sitemap|About US| Contact US: help@patsnap.com