Magnesium alloy crankcase and bearing bush matching structure
A crankcase body and matching structure technology, which is applied in the direction of engine components, machines/engines, casings, etc., can solve the problems of loose sliding between the bearing bush and the crankcase bearing, the reduction of the oil film thickness of the main bush, and the impact on the operation and life of the engine, etc., to achieve Lubricating oil is smooth, the weight of the whole machine is reduced, and the effect of improving the tightness of fit
- Summary
- Abstract
- Description
- Claims
- Application Information
AI Technical Summary
Problems solved by technology
Method used
Image
Examples
Embodiment 1
[0018] This embodiment provides a magnesium alloy crankcase body and bearing pad cooperation structure, the structure is as follows Figure 1-3 As shown, it includes a crankcase 1, a bushing 2 and a bearing bush 3. The bushing 2 is nested between the crankcase 1 and the bearing bush 3, and the crankcase 1 and the bearing bush 3 are connected through the bushing 2. The outer wall surface of the bushing 2 There is an involute spline 4 on it, and one end of the bush 2 is connected with the bearing hole on the crankcase 1 through an interference connection, and the other end of the bush 2 is connected through the bush 2 The inner ring and the bearing bush 3 are connected by an interference connection. There is an oil hole in the middle of the bush, and oil holes are also arranged on the crankcase and the bearing bush, and the axial positions of the oil holes on the crankcase, the bush and the bearing bush are consistent. The box is made of ZM6 magnesium alloy material, the bushing...
PUM
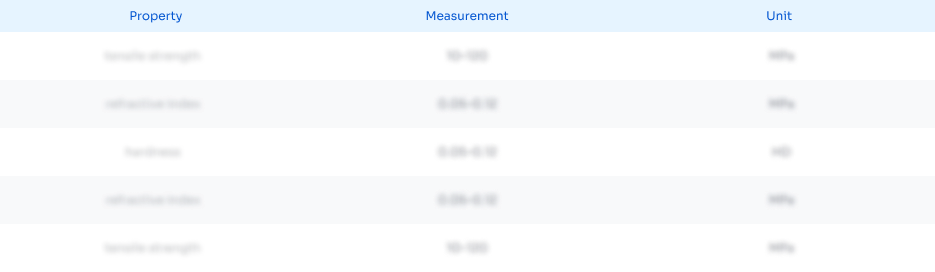
Abstract
Description
Claims
Application Information

- R&D
- Intellectual Property
- Life Sciences
- Materials
- Tech Scout
- Unparalleled Data Quality
- Higher Quality Content
- 60% Fewer Hallucinations
Browse by: Latest US Patents, China's latest patents, Technical Efficacy Thesaurus, Application Domain, Technology Topic, Popular Technical Reports.
© 2025 PatSnap. All rights reserved.Legal|Privacy policy|Modern Slavery Act Transparency Statement|Sitemap|About US| Contact US: help@patsnap.com