A processing method of partial double-alloy composite aluminum profile
A technology of alloy profiles and processing methods, which is applied in the field of processing local double-alloy composite aluminum profiles, can solve the problems of uneven thickness of alloy layers, blockage of parallel flow pipe holes, and high production costs, so as to reduce scrap rate, ensure reliability and The effect of stability and fewer processes
- Summary
- Abstract
- Description
- Claims
- Application Information
AI Technical Summary
Problems solved by technology
Method used
Image
Examples
Embodiment 1
[0041] Such as figure 1As shown, the present invention provides a processing method 100 for a partial double-alloy composite aluminum profile, the partial double-alloy composite aluminum profile includes a first alloy profile and a second alloy profile, the first alloy profile is extruded by an extrusion machine, and the second The second alloy profile is pre-processed and wound onto the coil. When the first alloy profile is extruded, the second alloy profile is compounded on the first alloy profile. As the second alloy profile is continuously extruded, the second alloy profile The profile is also continuously compounded on the surface of the first alloy profile under the rotation of the coiling disc to form the final partial double-alloy composite aluminum profile.
[0042] The processing method 100 includes:
[0043] Forming step 101: extruding and forming the first alloy profile with an extruder;
[0044] Feeding step 102: winding the pre-processed second alloy profile on...
Embodiment 2
[0052] The difference between this embodiment and the first embodiment is that the compounding step also includes a pressing process.
[0053] Processing method 100 in the present embodiment, as figure 2 As shown, the details are as follows:
[0054] Forming step 101: extruding and forming the first alloy profile with an extruder;
[0055] Feeding step 102: winding the pre-processed second alloy profile on the coil, and transporting the second alloy profile to the extrusion position of the first alloy profile through the coil wound with the second alloy profile;
[0056] Composite step 103: when the first alloy profile is extruded, the second alloy profile immediately covers the surface of the first alloy profile, so that the second alloy profile adheres to the first alloy profile under the residual temperature of the first alloy profile surface, thereby compounding the first alloy profile and the second alloy profile together;
[0057] Punching step 104: After the first a...
PUM
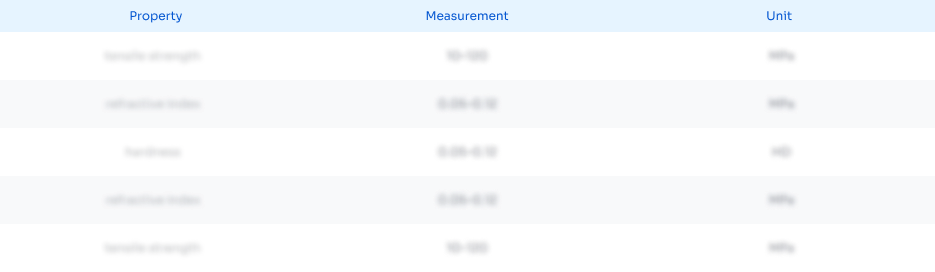
Abstract
Description
Claims
Application Information

- R&D
- Intellectual Property
- Life Sciences
- Materials
- Tech Scout
- Unparalleled Data Quality
- Higher Quality Content
- 60% Fewer Hallucinations
Browse by: Latest US Patents, China's latest patents, Technical Efficacy Thesaurus, Application Domain, Technology Topic, Popular Technical Reports.
© 2025 PatSnap. All rights reserved.Legal|Privacy policy|Modern Slavery Act Transparency Statement|Sitemap|About US| Contact US: help@patsnap.com