Unmanned transfer forklift based on laser positioning and stereoscopic vision and navigation method
A laser positioning and stereo vision technology, applied in two-dimensional position/channel control, vehicle position/route/altitude control, lifting device and other directions, which can solve the problems of inability to complete pickup, poor navigation accuracy in dead corners, and large manpower. Achieve the effect of avoiding damaged bags, improving loading efficiency, and high positioning accuracy
- Summary
- Abstract
- Description
- Claims
- Application Information
AI Technical Summary
Problems solved by technology
Method used
Image
Examples
Embodiment Construction
[0069] The present invention will be described in detail below in conjunction with the accompanying drawings and specific embodiments, where the schematic embodiments and descriptions of the present invention are used to explain the present invention, but not to limit the present invention.
[0070] Such as figure 1 , figure 2 As shown, an unmanned transfer forklift based on laser positioning and stereo vision of the present invention includes a forklift body 1 and several reflective targets 8 (laser reflective targets and pallet targets) arranged in the working environment of the forklift body. The forklift body includes a control mechanism located at its front part and a multi-pin ejector 7 at its rear part.
[0071] Such as image 3 As shown, the control mechanism includes an industrial computer processing module 3 and a battery, and the industrial computer processing module is respectively connected with a wireless communication module 2, a vehicle body controller, a la...
PUM
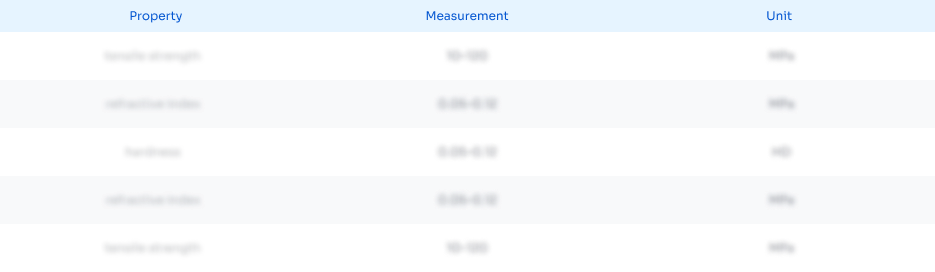
Abstract
Description
Claims
Application Information

- R&D Engineer
- R&D Manager
- IP Professional
- Industry Leading Data Capabilities
- Powerful AI technology
- Patent DNA Extraction
Browse by: Latest US Patents, China's latest patents, Technical Efficacy Thesaurus, Application Domain, Technology Topic, Popular Technical Reports.
© 2024 PatSnap. All rights reserved.Legal|Privacy policy|Modern Slavery Act Transparency Statement|Sitemap|About US| Contact US: help@patsnap.com