Aluminum alloy produced with metal casting technology and ingot casting method
A technology for aluminum alloy ingot and aluminum alloy, applied in the field of metal melting and casting process, can solve the problems of increasing tensile strength and hardness, aluminum liquid splashing, agglomeration, etc., to increase tensile strength and hardness, improve gloss and ductility , the effect of reducing the amount of splash
- Summary
- Abstract
- Description
- Claims
- Application Information
AI Technical Summary
Problems solved by technology
Method used
Image
Examples
Embodiment 1
[0034] An aluminum alloy produced by a metal melting and casting process, the components include Si, Fe, Ni, V, Na, Mg, Bi, Al and impurities, and the weight ratio of the above components is Si: 4%, Fe: 4% , Ni: 1%, V: 3%, Na: 2%, Mg: 2%, and Bi: 1%, and the balance consists of Al and 0.5% of impurities.
[0035] A method for casting an aluminum alloy ingot produced by a metal melting and casting process, comprising the steps of:
[0036] Step S1: Put all Si, Fe, Ni, V, Mg, Al and impurities into the furnace. After the smelting is completed, refine again. After refining, remove the aluminum ash on the surface of the molten aluminum in the furnace, clean up the site, and remove slag Finally, close the furnace door, prohibit any other operations on the molten aluminum in the furnace, and let it stand for 15 minutes to prevent secondary oxidation of the molten aluminum in the furnace;
[0037]Si and Fe are good for strengthening aluminum alloy; Ni has the effect of increasing te...
Embodiment 2
[0054] An aluminum alloy produced by a metal melting and casting process, the components include Si, Fe, Ni, V, Na, Mg, Bi, Al and impurities, and the weight ratio of the above components is Si: 8%, Fe: 5% , Ni: 2%, V: 4%, Na: 4%, Mg: 4.5%, and Bi: 2%, and the balance consists of Al and 0.7% of impurities.
[0055] A method for casting an aluminum alloy ingot produced by a metal melting and casting process, comprising the steps of:
[0056] Step S1: Put all Si, Fe, Ni, V, Mg, Al and impurities into the furnace. After the smelting is completed, refine again. After refining, remove the aluminum ash on the surface of the molten aluminum in the furnace, clean up the site, and remove slag Finally, close the furnace door, prohibit any other operations on the molten aluminum in the furnace, and let it stand for 15 minutes to prevent secondary oxidation of the molten aluminum in the furnace;
[0057] Si and Fe are good for strengthening aluminum alloy; Ni has the effect of increasing...
Embodiment 3
[0074] An aluminum alloy produced by a metal melting and casting process, the components include Si, Fe, Ni, V, Na, Mg, Bi, Al and impurities, and the weight ratio of the above components is Si: 12%, Fe: 6% , Ni: 3%, V: 5%, Na: 6%, Mg: 6% and Bi: 3%, and the balance consists of Al and 1% impurities.
[0075] A method for casting an aluminum alloy ingot produced by a metal melting and casting process, comprising the steps of:
[0076] Step S1: Put all Si, Fe, Ni, V, Mg, Al and impurities into the furnace. After the smelting is completed, refining is carried out. After refining, the aluminum ash on the surface of the molten aluminum in the furnace is cleaned, the site is cleaned, and the slag Finally, close the furnace door, prohibit any other operations on the molten aluminum in the furnace, and let it stand for 15 minutes to prevent secondary oxidation of the molten aluminum in the furnace;
[0077] Si and Fe are good for strengthening aluminum alloy; Ni has the effect of inc...
PUM
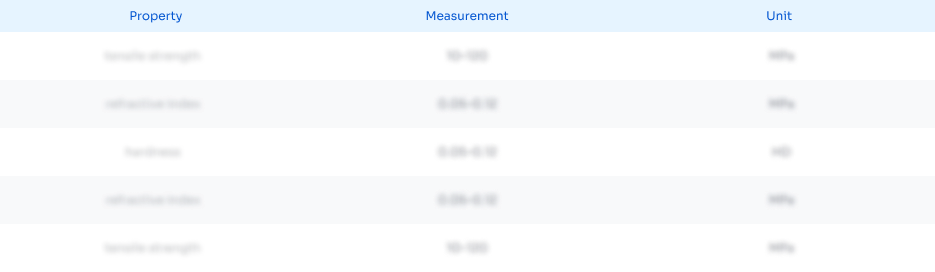
Abstract
Description
Claims
Application Information

- R&D
- Intellectual Property
- Life Sciences
- Materials
- Tech Scout
- Unparalleled Data Quality
- Higher Quality Content
- 60% Fewer Hallucinations
Browse by: Latest US Patents, China's latest patents, Technical Efficacy Thesaurus, Application Domain, Technology Topic, Popular Technical Reports.
© 2025 PatSnap. All rights reserved.Legal|Privacy policy|Modern Slavery Act Transparency Statement|Sitemap|About US| Contact US: help@patsnap.com