Tool connecting structure
A connection structure and cutting tool technology, applied in the direction of manufacturing tools, bonding grinding wheels, using vibrating fluid, etc., can solve problems such as cost increase, scratches, and impact on the service life of the cutter body, to ensure processing quality and buffer cutting collisions Effect
- Summary
- Abstract
- Description
- Claims
- Application Information
AI Technical Summary
Problems solved by technology
Method used
Image
Examples
Embodiment Construction
[0035] The technical solutions of the present invention will be clearly and completely described below in conjunction with the accompanying drawings. Apparently, the described embodiments are some of the embodiments of the present invention, but not all of them. Based on the embodiments of the present invention, all other embodiments obtained by persons of ordinary skill in the art without making creative efforts belong to the protection scope of the present invention. It should be noted that, in the case of no conflict, the embodiments of the present application and the features in the embodiments can be combined with each other.
[0036] The present invention will be further explained below in combination with specific embodiments.
[0037] refer to Figure 1 to Figure 7 , the tool connection structure provided by the embodiment of the present invention includes:
[0038] Ultrasonic cutter body 100, the first end of which is used to connect with the spindle of the machine ...
PUM
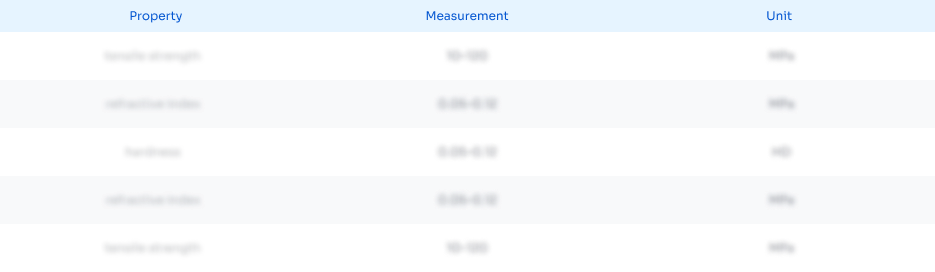
Abstract
Description
Claims
Application Information

- R&D
- Intellectual Property
- Life Sciences
- Materials
- Tech Scout
- Unparalleled Data Quality
- Higher Quality Content
- 60% Fewer Hallucinations
Browse by: Latest US Patents, China's latest patents, Technical Efficacy Thesaurus, Application Domain, Technology Topic, Popular Technical Reports.
© 2025 PatSnap. All rights reserved.Legal|Privacy policy|Modern Slavery Act Transparency Statement|Sitemap|About US| Contact US: help@patsnap.com