Double-slag-method smelting process
A double-slag method and process technology, which is applied in the direction of improving process efficiency and manufacturing converters, can solve the problems of difficult pouring of slag, poor dephosphorization effect, and long smelting cycle, so as to avoid overoxidation of molten steel and shorten smelting cycle , The effect of low phosphorus content in molten steel
- Summary
- Abstract
- Description
- Claims
- Application Information
AI Technical Summary
Problems solved by technology
Method used
Examples
Embodiment 1
[0069] In this embodiment, the experiment of a 500kg induction furnace is taken as an example, the charging amount of molten iron is 400kg, two branches are blown at the bottom, and the conditions of molten iron are: Si=0.3%, Mn=0.2%, P=0.12%, C=4.3%;
[0070] Top-bottom combined oxygen blowing rapid desiliconization and demanganization stage: gun position 20cm, top blowing oxygen flow rate 1.6Nm 3 / min, bottom blowing oxygen flow rate is 0.6Nm 3 / min, the oxygen blowing time of top blowing oxygen and bottom blowing oxygen is 1.5min;
[0071] Top-blown oxygen, bottom-blown inert gas dephosphorization stage: gun position 30cm, top-blown oxygen flow rate 1.2Nm 3 / min, bottom blowing nitrogen flow rate is 0.25Nm 3 / min, at the same time, the amount of lime powder sprayed by bottom blowing is 3kg, and the oxygen blowing time and nitrogen blowing time are both 3min.
[0072] Foaming dephosphorization slag control stage: gun position 25cm, oxygen flow rate 1.0Nm 3 / min, bottom b...
Embodiment 2
[0083] In this embodiment, the experiment of a 50t converter is taken as an example, the molten iron load is 45t, bottom blowing 4 branches, molten iron conditions: Si = 0.5%, Mn = 0.2%, P = 0.14%, C = 4.5%;
[0084] Top-bottom combined oxygen blowing rapid desiliconization and demanganization stage: gun position 1.5m, top blowing oxygen flow rate 135Nm 3 / min, bottom blowing oxygen flow rate is 36Nm 3 / min, the oxygen blowing time of top-blown oxygen and bottom-blown oxygen is 1.5min;
[0085] Top-blown oxygen, bottom-blown inert gas dephosphorization stage: gun position 3.0m, top-blown oxygen flow rate 90Nm 3 / min, bottom blowing nitrogen flow rate is 9Nm 3 / min, and at the same time, 600kg of limestone powder is blown at the bottom, and the oxygen blowing time and nitrogen blowing time are both 4min.
[0086] Foaming dephosphorization slag control stage: 50s before the end of the dephosphorization period, the oxygen flow rate at 2.0m of the gun position is 90Nm 3 / min, ...
Embodiment 3
[0097] In this embodiment, the experiment of a 50t converter is taken as an example, the molten iron load is 45t, bottom blowing 4 branches, molten iron conditions: Si = 0.55%, Mn = 0.21%, P = 0.16%, C = 4.43%;
[0098] Top-bottom combined oxygen blowing rapid desiliconization and demanganization stage: gun position 2.0m, top blowing oxygen flow rate 180Nm 3 / min, bottom blowing oxygen flow rate is 67.5Nm 3 / min, the oxygen blowing time of top blowing oxygen and bottom blowing oxygen is 80s;
[0099] Top blowing oxygen, bottom blowing inert gas dephosphorization stage: gun position 5.0m, oxygen flow rate 135Nm 3 / min, bottom blowing nitrogen flow rate is 36Nm 3 / min, and at the same time, 250kg of lime powder is blown at the bottom, and the oxygen blowing time and nitrogen blowing time are both 3.5min.
[0100] Foaming dephosphorization slag control stage: 100s before the end of the dephosphorization period, gun position 3.0m, oxygen flow rate 135Nm 3 / min, bottom blowing...
PUM
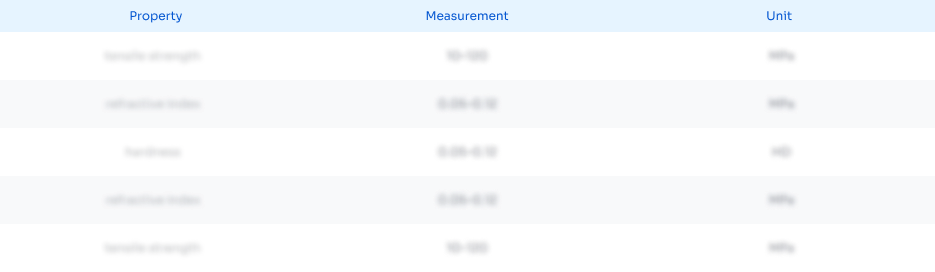
Abstract
Description
Claims
Application Information

- R&D
- Intellectual Property
- Life Sciences
- Materials
- Tech Scout
- Unparalleled Data Quality
- Higher Quality Content
- 60% Fewer Hallucinations
Browse by: Latest US Patents, China's latest patents, Technical Efficacy Thesaurus, Application Domain, Technology Topic, Popular Technical Reports.
© 2025 PatSnap. All rights reserved.Legal|Privacy policy|Modern Slavery Act Transparency Statement|Sitemap|About US| Contact US: help@patsnap.com