The Method of Removing Cracks on the Inner Cavity Surface of Selective Laser Melting Formed Parts
A technology of selective laser melting and surface cracking, which is applied to the improvement of process efficiency, additive manufacturing, and energy efficiency. It can solve the problems of complexity, high processing position limitations, and no effect of surface opening cracks, so as to improve surface roughness. , good repeatability and high surface quality results
- Summary
- Abstract
- Description
- Claims
- Application Information
AI Technical Summary
Problems solved by technology
Method used
Image
Examples
Embodiment Construction
[0024] The technical solutions of the present invention will be described in further detail below with reference to the accompanying drawings and embodiments.
[0025] The specific embodiments of the present invention are for the convenience of further description of the concept of the present invention, the technical problems to be solved, the technical features constituting the technical solution and the technical effects brought about. It should be noted that the description of these embodiments does not constitute a limitation of the present invention. In addition, the technical features involved in the embodiments of the present invention described below may be combined with each other as long as they do not conflict with each other.
[0026] In a schematic embodiment of the method for removing cracks on the surface of the inner cavity of the selected laser melting forming part of the present invention, as figure 1 As shown, the method includes:
[0027] Hot isostatic p...
PUM
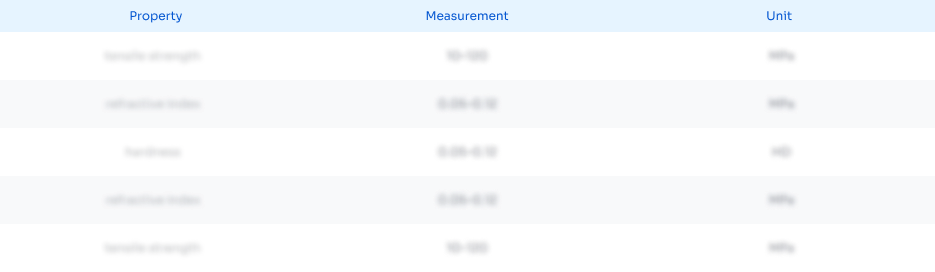
Abstract
Description
Claims
Application Information

- R&D
- Intellectual Property
- Life Sciences
- Materials
- Tech Scout
- Unparalleled Data Quality
- Higher Quality Content
- 60% Fewer Hallucinations
Browse by: Latest US Patents, China's latest patents, Technical Efficacy Thesaurus, Application Domain, Technology Topic, Popular Technical Reports.
© 2025 PatSnap. All rights reserved.Legal|Privacy policy|Modern Slavery Act Transparency Statement|Sitemap|About US| Contact US: help@patsnap.com