Welding spot defect detection system based on machine vision
A defect detection and machine vision technology, applied in the field of defect detection, can solve problems such as excessive current, perforation of weldments, poor stability of algorithm parameters, etc., and achieve the effect of high detection efficiency and detection accuracy
- Summary
- Abstract
- Description
- Claims
- Application Information
AI Technical Summary
Problems solved by technology
Method used
Image
Examples
Embodiment Construction
[0024] The present invention will be further described in conjunction with the following application scenarios.
[0025] see figure 1 , in this embodiment, a machine vision-based solder joint defect detection system is provided, including an image acquisition device, a control system, and a processing system; the solder joint defect detection system is mainly used for detecting solder joint defects on electronic products , the welding object is irregularly arranged solder joints on stainless steel; the stainless steel is 90 mm long and 40 mm wide, and solder joints are produced after being welded by a spot welding machine; the image acquisition device is used to collect images of the surface of the detected electronic product The collected image is transmitted to the processing system through data; the processing system is connected to the image collection device, receives the collected image and processes it, and identifies and judges the defects of solder joints in the image...
PUM
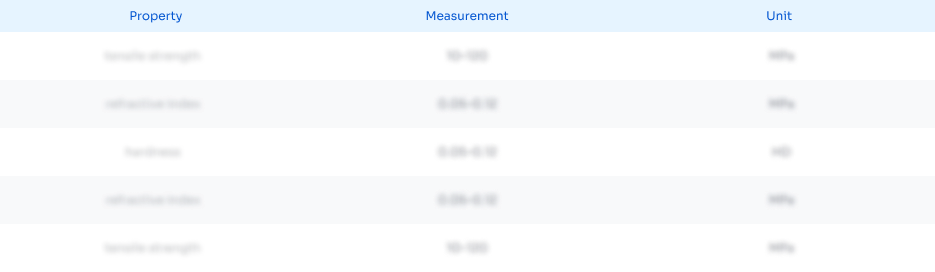
Abstract
Description
Claims
Application Information

- R&D Engineer
- R&D Manager
- IP Professional
- Industry Leading Data Capabilities
- Powerful AI technology
- Patent DNA Extraction
Browse by: Latest US Patents, China's latest patents, Technical Efficacy Thesaurus, Application Domain, Technology Topic, Popular Technical Reports.
© 2024 PatSnap. All rights reserved.Legal|Privacy policy|Modern Slavery Act Transparency Statement|Sitemap|About US| Contact US: help@patsnap.com