Three-dimensional laser scanner and camera calibration method based on geometric constraint
A three-dimensional laser and laser scanning technology, applied in the direction of instruments, optical devices, measuring devices, etc., can solve problems such as affecting calibration accuracy, lack of development and utilization of geometric constraints of point, line and surface, robustness and accuracy need to be improved, etc.
- Summary
- Abstract
- Description
- Claims
- Application Information
AI Technical Summary
Problems solved by technology
Method used
Image
Examples
Embodiment Construction
[0082] The present invention will be further described below in conjunction with accompanying drawing.
[0083] Such as figure 1 As shown, a 3D laser scanner and camera external calibration method based on geometric constraints includes the following steps:
[0084] Step 1. Make a calibration board. The size of the calibration board is 72cm×72cm, and black and white grids with a side length of 6cm are evenly distributed on it, such as figure 2 shown.
[0085] Step 2. Collect the 3D point cloud and 2D image of the calibration board, fix the 3D laser scanner and camera, face the calibration board to the 3D laser scanner and camera, scan the calibration board with the 3D laser scanner, and obtain the 3D point cloud of the calibration board, At the same time, use the camera to shoot the calibration board to obtain the two-dimensional image of the calibration board; change the pose of the calibration board, continue to scan and shoot the calibration board, so as to obtain a set ...
PUM
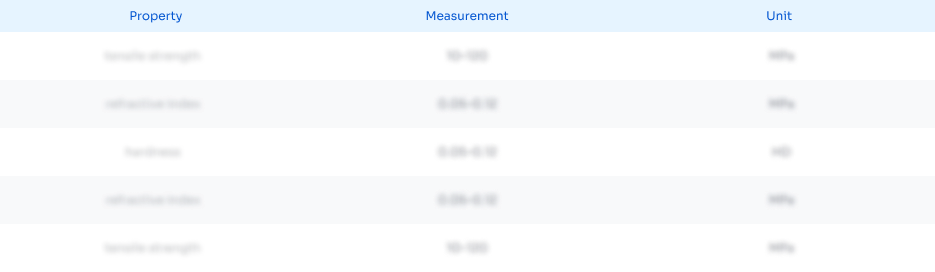
Abstract
Description
Claims
Application Information

- R&D
- Intellectual Property
- Life Sciences
- Materials
- Tech Scout
- Unparalleled Data Quality
- Higher Quality Content
- 60% Fewer Hallucinations
Browse by: Latest US Patents, China's latest patents, Technical Efficacy Thesaurus, Application Domain, Technology Topic, Popular Technical Reports.
© 2025 PatSnap. All rights reserved.Legal|Privacy policy|Modern Slavery Act Transparency Statement|Sitemap|About US| Contact US: help@patsnap.com