A modified cement engineering material with waterproof and anti-crack performance
An engineering material and cement technology, applied in the field of new functional materials, can solve the problems of water resistance, weak corrosion resistance, poor elongation, poor durability, etc., and achieve the effect of improving waterproof and corrosion resistance, reducing porosity and strong weather resistance.
- Summary
- Abstract
- Description
- Claims
- Application Information
AI Technical Summary
Problems solved by technology
Method used
Image
Examples
Embodiment 1
[0018] A modified cement engineering material with waterproof and anti-crack performance, which is made of the following components in parts by weight: 340 parts of cement, 15 parts of ammonium dihydrogen phosphate solution, 7.5 parts of polyethylene glycol, 2.0 parts of modifier, sulfuric acid 0.45 part of magnesium, 0.35 part of emulsifier, 0.25 part of solidifying agent, 0.15 part of defoamer, 200 parts of water; the preparation method of described modifying agent comprises the following steps:
[0019] (1) Add 35 ml of glycerin and 0.6 g of boron trifluoride to the three-necked flask, stir and mix for 30 minutes, then heat in a water bath to 70°C, add 28 g of epichlorohydrin dropwise to the flask, and control the dropping rate to 1.2 g / Minutes, after the dropwise addition, stir and react at a speed of 400 rpm for 55 minutes to obtain a viscous liquid, cool down to 60°C, add sodium carbonate solution to adjust the pH value in the range of 7.5-7.6, add 35 ml of absolute etha...
Embodiment 2
[0027] A modified cement engineering material with waterproof and anti-crack performance, which is made of the following components in parts by weight: 345 parts of cement, 16 parts of ammonium dihydrogen phosphate solution, 7.8 parts of polyethylene glycol, 2.2 parts of modifier, sulfuric acid 0.48 part of magnesium, 0.37 part of emulsifier, 0.28 part of solidifying agent, 0.18 part of defoamer, 205 parts of water; the preparation method of described modifying agent comprises the following steps:
[0028] (1) Add 38 ml of glycerin and 0.65 g of boron trifluoride to the three-necked flask, stir and mix for 35 minutes, then heat in a water bath to 72°C, add 29 g of epichlorohydrin dropwise to the flask, and control the dropping rate to 1.25 g / Minutes, after the dropwise addition, stir and react at a speed of 450 rpm for 58 minutes to obtain a viscous liquid, cool to 62°C, add sodium carbonate solution to adjust the pH value in the range of 7.5-7.6, add 38 ml of absolute ethanol...
Embodiment 3
[0036]A modified cement engineering material with waterproof and anti-crack performance, which is made of the following components in parts by weight: 350 parts of cement, 18 parts of ammonium dihydrogen phosphate solution, 8.0 parts of polyethylene glycol, 2.4 parts of modifier, sulfuric acid 0.50 part of magnesium, 0.38 part of emulsifier, 0.30 part of solidifying agent, 0.20 part of defoamer, 210 parts of water; the preparation method of described modifying agent comprises the following steps:
[0037] (1) Add 40 ml of glycerin and 0.7 g of boron trifluoride to a three-necked flask, stir and mix for 40 minutes, then heat in a water bath to 75°C, add 30 g of epichlorohydrin dropwise to the flask, and control the dropping rate to 1.3 g / Minutes, after the dropwise addition, stir and react at a speed of 500 rpm for 60 minutes to obtain a viscous liquid, cool down to 65°C, add sodium carbonate solution to adjust the pH value in the range of 7.5-7.6, add 40 ml of absolute ethanol...
PUM
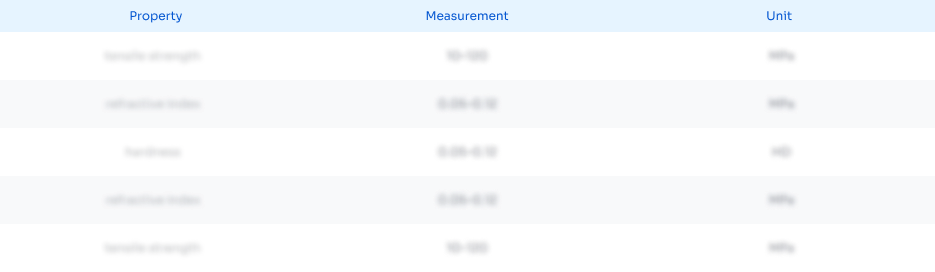
Abstract
Description
Claims
Application Information

- Generate Ideas
- Intellectual Property
- Life Sciences
- Materials
- Tech Scout
- Unparalleled Data Quality
- Higher Quality Content
- 60% Fewer Hallucinations
Browse by: Latest US Patents, China's latest patents, Technical Efficacy Thesaurus, Application Domain, Technology Topic, Popular Technical Reports.
© 2025 PatSnap. All rights reserved.Legal|Privacy policy|Modern Slavery Act Transparency Statement|Sitemap|About US| Contact US: help@patsnap.com