Method for detecting motor rotor position and rotation speed based on adaptive sliding mode observer
A technology of self-adaptive sliding mode and motor rotor, which is used in the control of generators, motor generators, and electromechanical transmissions.
- Summary
- Abstract
- Description
- Claims
- Application Information
AI Technical Summary
Problems solved by technology
Method used
Image
Examples
Embodiment Construction
[0041] In order to make the technical means, creative features, goals and effects of the present invention easy to understand, the following embodiments will specifically describe a method for detecting the position and speed of the motor rotor based on an adaptive sliding mode observer in the present invention in conjunction with the accompanying drawings.
[0042] figure 1 It is a block diagram of a brushless DC motor speed and torque double closed-loop control system.
[0043] Such as figure 1 As shown, the system consists of brushless DC motor, three-phase inverter bridge, space vector pulse width modulation (SVPWM), speed regulator, current regulator, improved sliding mode observer, IPSO parameter identification, field oriented control (FOC) And so on, the field oriented control part includes Park transform, Clark transform, Park inverse transform. Since there is no speed sensor in the system, the stator voltage u in the two-phase static αβ coordinate system is obtained...
PUM
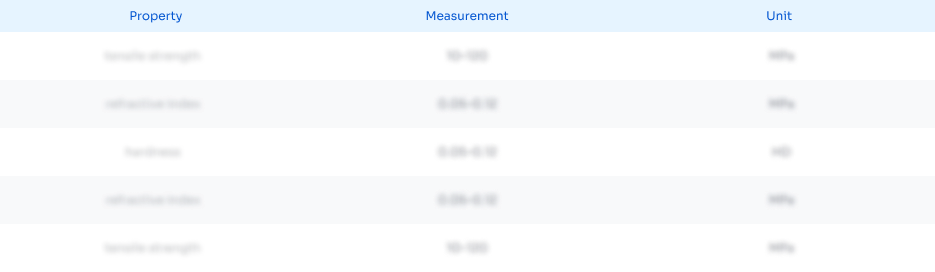
Abstract
Description
Claims
Application Information

- R&D
- Intellectual Property
- Life Sciences
- Materials
- Tech Scout
- Unparalleled Data Quality
- Higher Quality Content
- 60% Fewer Hallucinations
Browse by: Latest US Patents, China's latest patents, Technical Efficacy Thesaurus, Application Domain, Technology Topic, Popular Technical Reports.
© 2025 PatSnap. All rights reserved.Legal|Privacy policy|Modern Slavery Act Transparency Statement|Sitemap|About US| Contact US: help@patsnap.com