Continuous automatic collection process of textile fibers
An automatic finishing and textile fiber technology, which is applied in the direction of packaging, bundling machine parts, forming non-bunches, etc., can solve the problems of short fibers not being recycled and wasting resources, etc.
- Summary
- Abstract
- Description
- Claims
- Application Information
AI Technical Summary
Problems solved by technology
Method used
Image
Examples
Embodiment 1
[0096] 1. Such as figure 1 As shown, a continuous automatic finishing process for textile fibers is characterized by including:
[0097] Step 1, screening, the driving member 122 drives the fiber bundle to horizontally transmit along the discharge member 121, the blowing member 126 blows up the short fibers in the fiber bundle, and the first transmission member 123 picks up and transmits the short fibers to the second transmission member 124, the second transmission member 124 is transferred to the third transmission member 125;
[0098] Step two, the short fibers after shearing and screening are cut by the fixed cutting component 13 to the same length of the short fibers transferred to the cutting station by the third transmission member 125, and then the third transmission member 125 loosens the short fibers;
[0099] Step 3: Once gathered, the short fibers after shearing are collectively pushed to the condensing hole 234 by the gathering component 14;
[0100] Step four, forming, t...
PUM
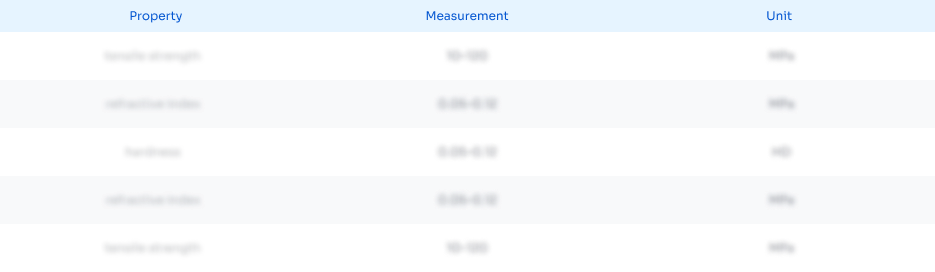
Abstract
Description
Claims
Application Information

- R&D Engineer
- R&D Manager
- IP Professional
- Industry Leading Data Capabilities
- Powerful AI technology
- Patent DNA Extraction
Browse by: Latest US Patents, China's latest patents, Technical Efficacy Thesaurus, Application Domain, Technology Topic, Popular Technical Reports.
© 2024 PatSnap. All rights reserved.Legal|Privacy policy|Modern Slavery Act Transparency Statement|Sitemap|About US| Contact US: help@patsnap.com