Flotation method of siliceous and calcareous collophanite
A technology of collophosite and silicon-calcium collophosphate, which is applied in the field of processing silica-calcium collophosphate by roasting reverse flotation technology, can solve the problems of immature technology, not being popularized and applied, and high production cost, and achieve simple and novel technology, Good flotation effect and low beneficiation cost
- Summary
- Abstract
- Description
- Claims
- Application Information
AI Technical Summary
Problems solved by technology
Method used
Examples
Embodiment 1
[0017] Embodiment 1, a kind of flotation method of siliceous calcareous collophosite, the method comprises the following steps:
[0018] (1) Calcining the crushed collophanite raw ore at 500°C; the calcination time is 2 hours;
[0019] (2) Feed the calcined ore into the mill, grind it to a suitable grinding fineness, and then feed it into the reverse flotation roughing mixing tank; the grinding fineness of the ore grinding operation is -74μm, and the raw ore accounts for 50 %;
[0020] (3) Add dispersants, inhibitors and collectors to the stirring tank for slurry adjustment; the dispersant is water glass; the inhibitor is starch compound; the collector is fatty acid soap Organic-like substances; the dosage is appropriate;
[0021] (4) The prepared ore pulp is sent to the reverse flotation roughing operation, the roughing foam is swept once, and the products in the tank are selected once, and finally the concentrate product is obtained.
Embodiment 2
[0022] Embodiment 2, a kind of flotation method of siliceous calcareous collophosite, the method comprises the following steps:
[0023] (1) Calcining the crushed collophanite raw ore at 950°C; the calcination time is 0.5h;
[0024] (2) Feed the calcined ore into the mill, grind it to a suitable grinding fineness, and then feed it into the reverse flotation roughing mixing tank; the grinding fineness of the ore grinding operation is -74μm, and the raw ore accounts for 90 %;
[0025] (3) Add dispersants, inhibitors and collectors to the stirring tank for slurry adjustment; the dispersant is water glass; the inhibitor is starch compound; the collector is fatty acid soap organic matter;
[0026] (4) The prepared ore pulp is sent to the reverse flotation roughing operation, the roughing foam is swept for 4 times, and the products in the tank are selected for 4 times, and finally the concentrate product is obtained.
Embodiment 3
[0027] Embodiment 3, a kind of flotation method of siliceous calcareous collophosite, the method comprises the following steps:
[0028] (1) Calcining the crushed collophanite raw ore at 600°C; the calcination time is 1h;
[0029] (2) Feed the calcined ore into the mill, grind it to a suitable grinding fineness, and then feed it into the reverse flotation roughing mixing tank; the grinding fineness of the ore grinding operation is -74μm, and the raw ore accounts for 70 %;
[0030] (3) Add dispersants, inhibitors and collectors to the stirring tank for slurry adjustment; the dispersant is water glass; the inhibitor is starch compound; the collector is fatty acid soap organic matter;
[0031] (4) The prepared ore pulp is sent to the reverse flotation roughing operation, the roughing foam is swept twice, and the product in the tank is sorted three times, and finally the concentrate product is obtained.
PUM
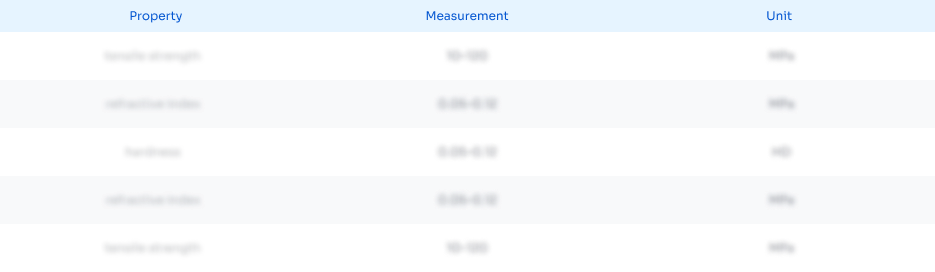
Abstract
Description
Claims
Application Information

- R&D
- Intellectual Property
- Life Sciences
- Materials
- Tech Scout
- Unparalleled Data Quality
- Higher Quality Content
- 60% Fewer Hallucinations
Browse by: Latest US Patents, China's latest patents, Technical Efficacy Thesaurus, Application Domain, Technology Topic, Popular Technical Reports.
© 2025 PatSnap. All rights reserved.Legal|Privacy policy|Modern Slavery Act Transparency Statement|Sitemap|About US| Contact US: help@patsnap.com