A plastic pellet granulator
A technology of plastic granules and granulator, applied in the field of plastic processing, can solve the problems of plastic granules sticking, non-uniform particle size of plastic granules, uncontrollable cooling effect, etc., to achieve the effect of ensuring uniformity
- Summary
- Abstract
- Description
- Claims
- Application Information
AI Technical Summary
Problems solved by technology
Method used
Image
Examples
Embodiment
[0025] A plastic pellet granulator, such as Figure 1-5 As shown, it includes a first mounting plate 1, a first collection frame 2, a support seat 3, an air-drying frame 4, a first bearing seat 6, a first pulley 7, a first flat belt 8, a first rotating shaft 9, and a fan blade 10 , the second pulley 11, the second rotating shaft 12, the second bearing housing 13, the cutter roller 15, the pelletizing frame 16, the third bearing housing 17, the first extrusion frame 18, the cooling pipe 19, the second extrusion frame 20 , extrusion screw 21, lower hopper 22, fourth bearing block 23, third pulley 24, second flat belt 25, fourth pulley 26, second mounting plate 27, third rotating shaft 28, fifth bearing block 29, motor 99. The fourth rotating shaft 77 and the third mounting plate 88; the second mounting plate 27 is fixed to one side of the first mounting plate 1, and the air-drying frame 4 is fixed to the first mounting plate 1 through the support seat 3, away from the second mou...
PUM
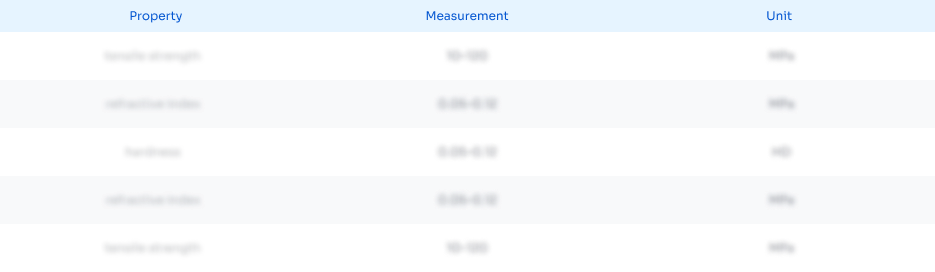
Abstract
Description
Claims
Application Information

- R&D
- Intellectual Property
- Life Sciences
- Materials
- Tech Scout
- Unparalleled Data Quality
- Higher Quality Content
- 60% Fewer Hallucinations
Browse by: Latest US Patents, China's latest patents, Technical Efficacy Thesaurus, Application Domain, Technology Topic, Popular Technical Reports.
© 2025 PatSnap. All rights reserved.Legal|Privacy policy|Modern Slavery Act Transparency Statement|Sitemap|About US| Contact US: help@patsnap.com