Nonlinear torsion modal ultrasonic guided-wave method used for evaluating metal circular tube microdamage
A torsional mode, ultrasonic guided wave technology, applied in the analysis of solids using sonic/ultrasonic/infrasonic waves, material analysis using sonic/ultrasonic/infrasonic waves, and processing response signals of detection, etc., which can solve the limited number of fundamental frequency modal points , use restrictions and other issues, to achieve the effect of facilitating analysis and processing, reducing noise, and high detection accuracy
- Summary
- Abstract
- Description
- Claims
- Application Information
AI Technical Summary
Problems solved by technology
Method used
Image
Examples
Embodiment Construction
[0030] In order to make the objects and advantages of the present invention clearer, the present invention will be further described in detail below in conjunction with the examples. It should be understood that the specific embodiments described here are only used to explain the present invention, not to limit the present invention.
[0031] The non-linear torsional mode ultrasonic guided wave evaluation method of circular pipe micro-damage of the present invention excites an ultrasonic signal of a certain frequency through the excitation / receiving unit, reduces noise through the impedance, connects the excitation transducer, and sends it to the test piece through the coupling agent. , the other end of the test piece is connected to the receiving transducer to detect the propagated guided wave signal, filtered by the receiving preamplifier and sent to the oscilloscope, and the signal is averaged 200-2000 times in the oscilloscope to improve the signal-to-noise ratio. Store th...
PUM
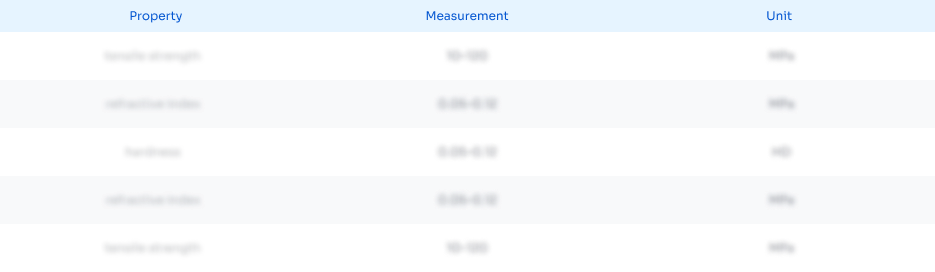
Abstract
Description
Claims
Application Information

- Generate Ideas
- Intellectual Property
- Life Sciences
- Materials
- Tech Scout
- Unparalleled Data Quality
- Higher Quality Content
- 60% Fewer Hallucinations
Browse by: Latest US Patents, China's latest patents, Technical Efficacy Thesaurus, Application Domain, Technology Topic, Popular Technical Reports.
© 2025 PatSnap. All rights reserved.Legal|Privacy policy|Modern Slavery Act Transparency Statement|Sitemap|About US| Contact US: help@patsnap.com