Mixing method for removing impurities of thickener before loading
A paste and impurity technology, which is applied in the mixing field of removing paste impurities before loading, can solve the problem of uneven density between the top and bottom of the paste, and achieve the goals of improving screening efficiency, improving mixing uniformity, and improving dispersing and mixing efficiency Effect
- Summary
- Abstract
- Description
- Claims
- Application Information
AI Technical Summary
Problems solved by technology
Method used
Image
Examples
Embodiment 1
[0037] According to the drawings in the manual figure 1 The mixing method used in this example to remove paste impurities before charging is described.
[0038] A mixing method for removing paste impurities before charging, comprising the following steps:
[0039] (a) Preliminary mixing part, the paste to be mixed in the upper bin 1 is pushed up and mixed with the paste at the upper part through the stirring part 341 on the mixing mechanism 3 by moving up and down ;
[0040] (b) the transmission part, the paste after the preliminary mixing in the step (a) is transferred to the bottom by the rotating roller 231 in a rotating manner;
[0041] (c) Screening part, after the step (b), the paste enters the screening station, and the screen mesh 321 on the screening assembly 32 separates the impurities from the paste by vibration, and the bonded paste The material is dispersed, and the impurities are output along the screen 321 through the impurity outlet 311, and the paste passes...
Embodiment 2
[0052] According to the manual attached Figure 2-11 Describe the mixing system used to remove paste impurities before charging in Example 2.
[0053] Such as figure 2 , 3 , Shown in 4 and 5, the mixing method for removing paste impurities before charging, including feeding bin 1, also includes:
[0054] A feeding mechanism 2, the feeding mechanism 2 is communicated with the upper material bin 1, and it includes a material delivery chamber 21, which is arranged in the material delivery chamber 21 to transfer the paste in the upper material bin 1 to the next process. The conveying assembly 22 in the position and the rotating member 23 that drives the conveying assembly 22 to rotate; The chamber 21 transports the paste in the feeding bin 1 quantitatively and at a constant speed to the mixing bin 31;
[0055] Mixing mechanism 3, said mixing mechanism 3 includes a mixing bin 31 communicated with the interior of the material delivery chamber 21, a screening assembly 32 arrange...
PUM
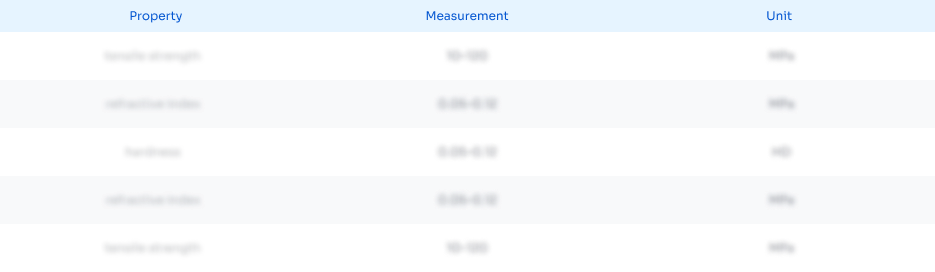
Abstract
Description
Claims
Application Information

- R&D
- Intellectual Property
- Life Sciences
- Materials
- Tech Scout
- Unparalleled Data Quality
- Higher Quality Content
- 60% Fewer Hallucinations
Browse by: Latest US Patents, China's latest patents, Technical Efficacy Thesaurus, Application Domain, Technology Topic, Popular Technical Reports.
© 2025 PatSnap. All rights reserved.Legal|Privacy policy|Modern Slavery Act Transparency Statement|Sitemap|About US| Contact US: help@patsnap.com