Production process of phthalocyanine blue series dye direct blue 199
A production process, the technology of phthalocyanine blue, which is applied in the field of dye production process, can solve the problems such as difficult membrane filtration and difficult treatment of filter press wastewater, and achieve the effects of increasing coloring effect, reducing dye cost, and reducing press filter wastewater production
- Summary
- Abstract
- Description
- Claims
- Application Information
AI Technical Summary
Problems solved by technology
Method used
Examples
Embodiment 1
[0018] A kind of production technology of phthalocyanine blue series dye Direct Blue 199, the steps are as follows:
[0019] (1) Sulfonation: In a 1000ml four-necked bottle, add 582.5g of chlorosulfonic acid, slowly add 103g of copper cyanine, stir and beat for 2 hours in a sealed state, raise the temperature to 135-140°C, keep warm for 3 hours, and slowly drop to At room temperature, use ice-out dyes, the temperature is lower than 5°C, filter the filter cake, wash with ice water until the filter cake pH = 4 to obtain 480g of sulfonylated filter cake (solid content 45%) for later use, the filter cake should be kept at a low temperature of about 5°C save;
[0020] (2) Condensation and ammonolysis: Add all the above-mentioned sulfonylated filter cakes into a 2000ml three-necked bottle, add 485g of industrial ammonia water and 95g of ethylene glycol, stir at room temperature for 4 hours, slowly raise the temperature to 42°C and keep the pH above 9, if it is low Add ammonia water...
Embodiment 2
[0024] A kind of production technology of phthalocyanine blue series dye Direct Blue 199, the steps are as follows:
[0025] (1) Sulfonation: In a 1000ml four-neck flask, add 566.5g of chlorosulfonic acid, slowly add 103g of copper cyanine, stir and beat for 1.5 hours in a sealed state, raise the temperature to 135°C, keep the reaction for 2.5 hours, and slowly cool down to room temperature, Use ice-out dyes, filter the filter cake at a temperature lower than 5°C, and wash the filter cake with ice water until the filter cake pH=4 to obtain 472g of sulfonylated filter cake (solid content 50%) for later use. The filter cake should be stored at a low temperature of about 5°C;
[0026] (2) Condensation and ammonolysis: Add all the above-mentioned sulfonylated filter cakes into a 2000ml three-necked bottle, add 566.4g of industrial ammonia water and 141.6g of ethylene glycol, stir at room temperature for 4 hours, slowly raise the temperature to 40°C to keep the pH above 9, If it is...
Embodiment 3
[0030] A kind of production technology of phthalocyanine blue series dye Direct Blue 199, the steps are as follows:
[0031] (1) Sulfonation: In a 1000ml four-neck flask, add 618g of chlorosulfonic acid, slowly add 103g of copper cyanine, stir and beat for 2.5 hours in a sealed state, raise the temperature to 140°C, keep the reaction for 3.5 hours, slowly cool down to room temperature, and use Ice out the dye, the temperature is lower than 5°C, and the filtered filter cake is washed with ice water until the filter cake pH=4 to obtain 486g of sulfonylated filter cake (solid content 48%) for later use, and the filter cake should be stored at a low temperature of about 5°C;
[0032] (2) Condensation and ammonolysis: Add all the above-mentioned sulfonylated filter cakes into a 2000ml three-necked bottle, add 729g of industrial ammonia water and 194.4g of ethylene glycol, stir at room temperature for 4 hours, slowly raise the temperature to 45°C to keep the pH above 9, if If it is ...
PUM
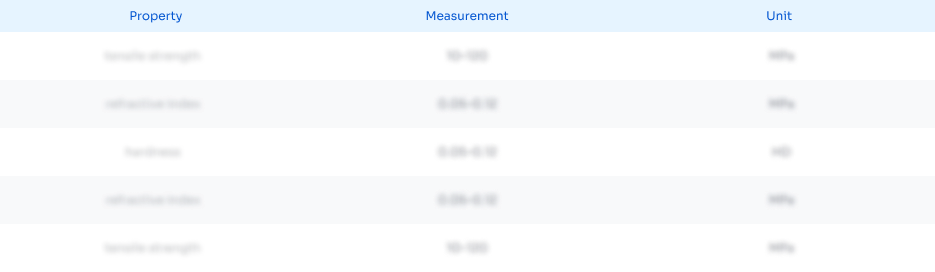
Abstract
Description
Claims
Application Information

- Generate Ideas
- Intellectual Property
- Life Sciences
- Materials
- Tech Scout
- Unparalleled Data Quality
- Higher Quality Content
- 60% Fewer Hallucinations
Browse by: Latest US Patents, China's latest patents, Technical Efficacy Thesaurus, Application Domain, Technology Topic, Popular Technical Reports.
© 2025 PatSnap. All rights reserved.Legal|Privacy policy|Modern Slavery Act Transparency Statement|Sitemap|About US| Contact US: help@patsnap.com