EPC disappearing die casting iron coating
A technology of lost foam casting and coating, which is applied in the direction of coating, casting mold, casting mold composition, etc. It can solve the problems of low strength, easy to be corroded by strong alkali, low air permeability, etc., so as to prolong the service life and avoid drying and cracking , increase the effect of air permeability
- Summary
- Abstract
- Description
- Claims
- Application Information
AI Technical Summary
Problems solved by technology
Method used
Examples
Embodiment 1
[0020] A kind of EPC lost foam cast iron coating, configure 100kg of EPC lost foam cast steel coating, including the following raw materials: 32.2kg of quartz sand, 32.2kg of bauxite, 1.92kg of bentonite, 1.0kg of attapulgite, 0.12kg of CMC, hexametaphosphoric acid Sodium 1.3kg, sodium carbonate 0.05kg and water 31.2kg.
[0021] A kind of preparation method of described EPC lost foam cast iron coating, comprises the following steps:
[0022] S1: Weigh the quartz sand according to the ratio, and divide the quartz sand into 5.5% A component, 43% B component, 46% C component and 4.5% D component according to the weight percentage, and then divide the four groups The divided quartz sand is crushed and ground separately, and different particle sizes are formed after grinding;
[0023] S2: Take the bauxite according to the ratio, and divide the bauxite into 14% E component, 19% F component, 23% G component and 44% H component according to the weight percentage, and then divide the ...
Embodiment 2
[0031] An EPC lost foam cast iron coating, equipped with 100kg of EPC lost foam cast steel coating, including the following raw materials: 41.78kg of quartz sand, 28.2kg of bauxite, 1.42kg of bentonite, 0.5kg of attapulgite, 0.07kg of CMC, hexametaphosphoric acid Sodium 0.8kg, sodium carbonate 0.02kg and water 27.2kg.
[0032] A kind of preparation method of described EPC lost foam cast iron coating, comprises the following steps:
[0033] S1: Weigh the quartz sand according to the ratio, and divide the quartz sand into 5.5% A component, 43% B component, 46% C component and 4.5% D component according to the weight percentage, and then divide the four groups The divided quartz sand is crushed and ground separately, and different particle sizes are formed after grinding;
[0034] S2: Take the bauxite according to the ratio, and divide the bauxite into 14% E component, 19% F component, 23% G component and 44% H component according to the weight percentage, and then divide the fo...
Embodiment 3
[0042] A kind of EPC lost foam cast iron coating, configure 100kg of EPC lost foam cast steel coating, including the following raw materials: 22.62kg of quartz sand, 36.2kg of bauxite, 2.42kg of bentonite, 1.5kg of attapulgite, 0.17kg of CMC, hexametaphosphoric acid Sodium 1.8kg, sodium carbonate 0.08kg and water 35.2kg.
[0043] A kind of preparation method of described EPC lost foam cast iron coating, comprises the following steps:
[0044] S1: Weigh the quartz sand according to the ratio, and divide the quartz sand into 5.5% A component, 43% B component, 46% C component and 4.5% D component according to the weight percentage, and then divide the four groups The divided quartz sand is crushed and ground separately, and different particle sizes are formed after grinding;
[0045] S2: Take the bauxite according to the ratio, and divide the bauxite into 14% E component, 19% F component, 23% G component and 44% H component according to the weight percentage, and then divide the f...
PUM
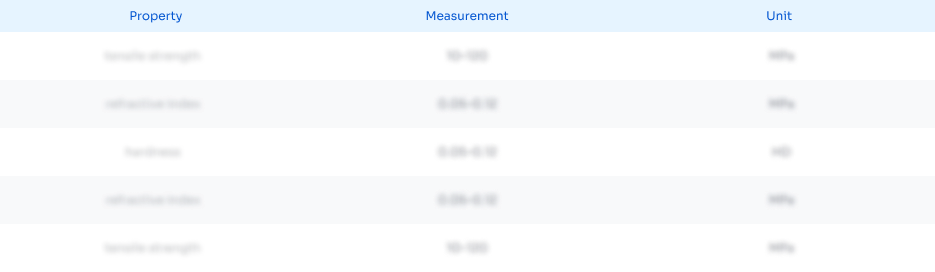
Abstract
Description
Claims
Application Information

- Generate Ideas
- Intellectual Property
- Life Sciences
- Materials
- Tech Scout
- Unparalleled Data Quality
- Higher Quality Content
- 60% Fewer Hallucinations
Browse by: Latest US Patents, China's latest patents, Technical Efficacy Thesaurus, Application Domain, Technology Topic, Popular Technical Reports.
© 2025 PatSnap. All rights reserved.Legal|Privacy policy|Modern Slavery Act Transparency Statement|Sitemap|About US| Contact US: help@patsnap.com