Grain processing method
A processing method and technology of grain, applied in grain processing, grain milling, application and other directions, can solve the problems of the angle of the sieve drum should not be too large, the separation efficiency is too small, and the material flow speed is accelerated, so as to reduce the content of impurities, The effect of good use and simple structure
- Summary
- Abstract
- Description
- Claims
- Application Information
AI Technical Summary
Problems solved by technology
Method used
Image
Examples
Embodiment 1
[0027] (1), first select the raw material wheat, and then clean the selected raw material wheat, the specific steps of cleaning are as follows:
[0028] a. First feed the raw wheat into the magnetic separator for magnetic separation, and then carry out preliminary cleaning and screening. The length of the sieve cylinder is 650mm, the angle of the sieve cylinder is 3°, and the diameter of the sieve hole is 4.0mm;
[0029] b. the wheat screened in step a is air-selected, and sent to the de-stoner for initial stone removal;
[0030] C. After step b, the stone-removed wheat is sent to the threshing machine for threshing, and then winnowed again. The specific steps of threshing are as follows:
[0031] ①. Check and turn on the wheat threshing machine in advance for idling;
[0032] ②. Control the feeding amount to gradually increase to normal;
[0033] ③. Stop feeding first, then close after discharging;
[0034] (2) The cleaned wheat is sent to the watering machine for watering...
Embodiment 2
[0038] (1), first select the raw material wheat, and then clean the selected raw material wheat, the specific steps of cleaning are as follows:
[0039] a. First feed the raw wheat into the magnetic separator for magnetic separation, and then carry out preliminary cleaning and screening. The length of the sieve cylinder is 650mm, the angle of the sieve cylinder is 3°, and the diameter of the sieve hole is 4.2mm;
[0040] b. the wheat screened in step a is air-selected, and sent to the de-stoner for initial stone removal;
[0041] C. After step b, the stone-removed wheat is sent to the threshing machine for threshing, and then winnowed again. The specific steps of threshing are as follows:
[0042] ①. Check and turn on the wheat threshing machine in advance for idling;
[0043] ②. Control the feeding amount to gradually increase to normal;
[0044] ③. Stop feeding first, then close after discharging;
[0045] (2) The cleaned wheat is sent to the watering machine for watering...
Embodiment 3
[0049] (1), first select the raw material wheat, and then clean the selected raw material wheat, the specific steps of cleaning are as follows:
[0050] a. First feed the raw wheat into the magnetic separator for magnetic separation, and then carry out preliminary cleaning screening. The length of the sieve cylinder is 650mm, the angle of the sieve cylinder is 3°, and the diameter of the sieve hole is 4.4mm;
[0051] b. the wheat screened in step a is air-selected, and sent to the de-stoner for initial stone removal;
[0052] C. After step b, the stone-removed wheat is sent to the threshing machine for threshing, and then winnowed again. The specific steps of threshing are as follows:
[0053] ①. Check and turn on the wheat threshing machine in advance for idling;
[0054] ②. Control the feeding amount to gradually increase to normal;
[0055] ③. Stop feeding first, then close after discharging;
[0056] (2) The cleaned wheat is sent to the watering machine for watering. An...
PUM
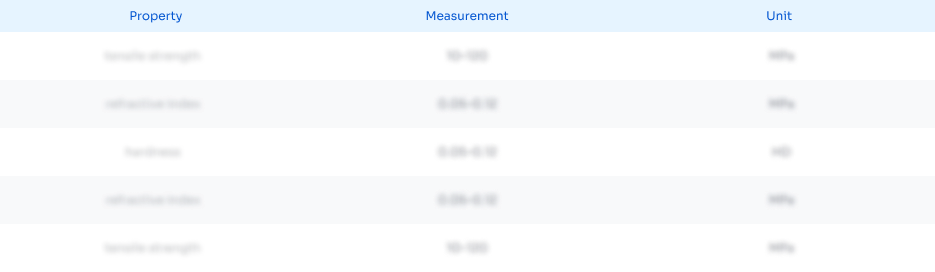
Abstract
Description
Claims
Application Information

- R&D Engineer
- R&D Manager
- IP Professional
- Industry Leading Data Capabilities
- Powerful AI technology
- Patent DNA Extraction
Browse by: Latest US Patents, China's latest patents, Technical Efficacy Thesaurus, Application Domain, Technology Topic, Popular Technical Reports.
© 2024 PatSnap. All rights reserved.Legal|Privacy policy|Modern Slavery Act Transparency Statement|Sitemap|About US| Contact US: help@patsnap.com