Shaping double-sided composite integrated machine
An all-in-one, double-sided technology, used in layered products, lamination devices, lamination and other directions, can solve the problems of increased work intensity, low work efficiency, energy consumption, etc., to ensure smoothness, reduce labor intensity, The effect of improving work efficiency
- Summary
- Abstract
- Description
- Claims
- Application Information
AI Technical Summary
Problems solved by technology
Method used
Image
Examples
Embodiment approach
[0030] like Figure 1 to Figure 3 It shows an embodiment of a stereotyped double-sided compound all-in-one machine of the present invention, including a cloth unloading station 1, a liquid rolling station 2, a shaping needle station 3, a drying station 4, and a TPU film placed in sequence Fitting station 5, fabric fitting station 6, needle removal station 7 and rolling station 8, a needle plate chain transmitted along the direction of the station is passed between the shaping needle station 3 and the needle removal station 7 9 moves, and each station and needle plate chain 9 realize synchronization by a main shaft transmission part, and needle plate chain 9 realizes horizontal conveyance by a left-right drive sprocket.
[0031] The cloth laying station 1 is equipped with a cloth laying support 11, and the cloth laying support 11 is equipped with a centering spreading device. The centering spreading device includes a plurality of cloth guide rollers A12, and two adjacent cloth ...
PUM
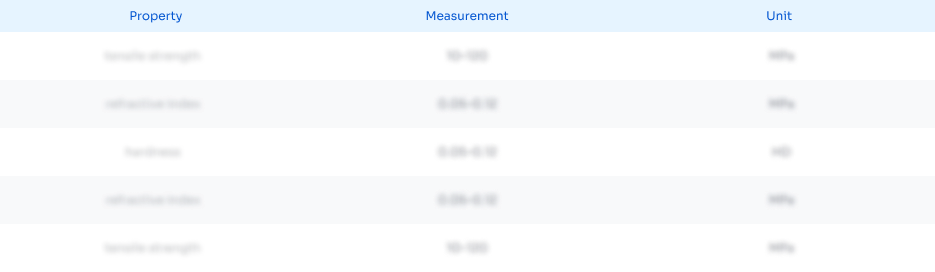
Abstract
Description
Claims
Application Information

- R&D Engineer
- R&D Manager
- IP Professional
- Industry Leading Data Capabilities
- Powerful AI technology
- Patent DNA Extraction
Browse by: Latest US Patents, China's latest patents, Technical Efficacy Thesaurus, Application Domain, Technology Topic, Popular Technical Reports.
© 2024 PatSnap. All rights reserved.Legal|Privacy policy|Modern Slavery Act Transparency Statement|Sitemap|About US| Contact US: help@patsnap.com