Self-adaptive welding system and method based on aluminum material
A technology of welding system and welding method, which is applied in the direction of welding power supply, welding equipment, welding monitoring device, etc., can solve the problems of welding pressure monitoring and welding quality can not be guaranteed, and achieve the goal of increasing productivity, improving connection quality and reducing production cost Effect
- Summary
- Abstract
- Description
- Claims
- Application Information
AI Technical Summary
Problems solved by technology
Method used
Image
Examples
Embodiment Construction
[0029] The embodiments of the present invention are described in detail below. This embodiment is implemented on the premise of the technical solution of the present invention, and detailed implementation methods and specific operating procedures are provided, but the protection scope of the present invention is not limited to the following implementation example.
[0030] Such as figure 1 As shown, an adaptive welding system based on aluminum materials, including: welding control cabinet, welding tongs, transformer, pressure sensor, electric cylinder, current sensor, voltage sensor, PC; welding control cabinet is connected with welding tongs, welding tongs Connect with transformer, pressure sensor and electric cylinder, connect transformer with current sensor and voltage sensor, connect PC with welding control cabinet; welding control cabinet includes pressure signal collector, leakage monitoring, power supply; pressure signal collector, leakage monitoring, power supply All ...
PUM
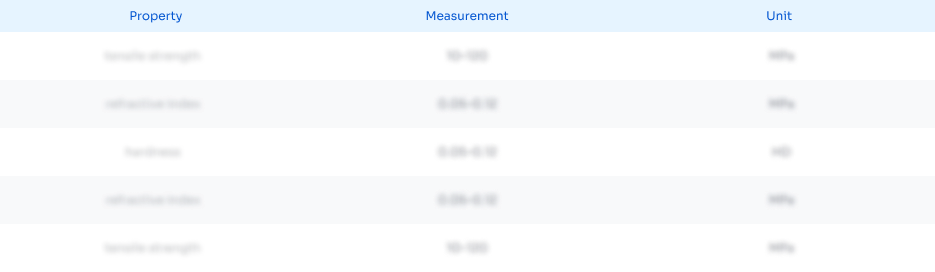
Abstract
Description
Claims
Application Information

- R&D Engineer
- R&D Manager
- IP Professional
- Industry Leading Data Capabilities
- Powerful AI technology
- Patent DNA Extraction
Browse by: Latest US Patents, China's latest patents, Technical Efficacy Thesaurus, Application Domain, Technology Topic, Popular Technical Reports.
© 2024 PatSnap. All rights reserved.Legal|Privacy policy|Modern Slavery Act Transparency Statement|Sitemap|About US| Contact US: help@patsnap.com